The Ecosystem of Industrial Robotics
Automation is not just about robots. There is a delicate and complex ecosystem surrounding the entire process that involves more than just the robot and the people manufacturing them.
Automation has become a driving force behind modern society, powering our homes, creating our cars, and handling our transportation systems. At the heart of this ecosystem are robots, marvels of engineering and technology that can be built to perform a wide range of tasks or handle a wide range of data.
However, automation is not just about robots. There is a delicate and complex ecosystem surrounding the entire process that involves more than just the robot and the people manufacturing them.
The Ecosystem
Behind robots is a network of engineers, designers, and technicians who build, program, maintain, sell, distribute, and integrate the robots into automation lines. These companies include robot manufacturers, end-effector manufacturers, moving equipment providers, tooling/jig manufacturers, sensor providers, software providers, integrators, certification organisations, and end users.

Robot Manufacturers
Traditionally, robot manufacturers do not sell directly to customers, but rather use integrators and resellers to distribute their products (These are the companies that act as intermediaries between the sellers and the end users. For instance, SYSAXES, which is specialised in collaborative robotics, esp. Universal Robots).
There are two main types of robots: industrial robots and collaborative robots, also known as cobots. Industrial robots are typically large, expensive, and require specialized training to operate. They are used in manufacturing and other industries for tasks such as welding, painting, and assembly. Cobots, on the other hand, are smaller, more affordable, and designed to work alongside humans in a collaborative environment, which is not always the case! They are used for tasks such as material handling, machine tending, and quality control.
End-effector Manufacturers
End-effectors are tools or devices that are attached to the end of a robot arm and are used to perform a specific task. These tasks can range from simple tasks such as gripping and manipulating objects, to more complex tasks such as welding or painting, suctioning, or pinching. End-effector manufacturers design and build these tools, which are then sold to resellers, integrators and customers to create complete automation systems for their customers. Some common examples of end-effectors include grippers, weld guns, and painting nozzles. These tools can be customised to meet the specific needs of the task being performed and the environment in which the robot will be operating.
Moving Equipment
Moving equipment refers to the devices used to transport materials within an automation system. This can include conveyor belts, automated guided vehicles (AGVs), and autonomous mobile robots (AMRs). Conveyor belts are mechanical devices that consist of a continuous moving belt supported by rollers or a flat pan along its path. They are used to transport materials from one place to another and can be customised to meet specific needs. AGVs are automated vehicles that use sensors and software to navigate around a facility and transport materials to and from various locations. AMRs are similar to AGVs, but they are typically smaller and more flexible, allowing them to navigate through tight spaces and around obstacles.
Tooling/jigs
Tooling and jigs refer to the fixtures and tools that are used to hold and manipulate parts or materials during the production process. They are often custom-made for specific tasks or products and can be quite expensive. In the context of automation, tooling and jigs can be used with robots to perform certain tasks or operations. However, using custom tooling and jigs can also constrain the production environment, as they are often specific to a particular process or product and cannot be easily adapted or modified. Additionally, because robots are limited by their programming and do not have the same level of adaptability as humans, they may require more specialised tooling and jigs in order to perform certain tasks, which can also increase the overall cost of automation.
Sensor providers
Sensor providers manufacture sensors that can be used by robots or automation systems for various purposes, such as quality control, robot guidance, or safety. Sensors can be used to gather data about the environment or the objects being manipulated by the robot, and this data can be used to make decisions or adjust the robot’s actions. Vision sensors (e.g. inbolt), which use cameras to gather data, are commonly used for quality control or robot guidance. Other types of sensors, such as proximity sensors or force sensors, can be used for safety purposes, such as to detect when a person enters a restricted area (e.g. Inxpect) or to prevent the robot from applying too much force to an object.
Software providers
Software providers are companies that develop and sell software specifically designed for use with industrial robots. These software programs allow users to program and control the movements and actions of their robots and can include features such as offline programming (e.g. RoboDK), which allows users to program their robots without the need to be physically near their robots at the same time. This can be useful to update a robot’s program without interrupting production, or to program multiple robots at a time. Some software providers also offer tools for simulation and visualisation, which can help users design and test their robotic systems before implementing them in a production environment.
Integrators
These are the companies that take the robots and other automation equipment from the sellers and integrate them into a complete system that is ready for use in the customer’s facility. They are responsible for installing the equipment, programming it to perform specific tasks, and providing ongoing maintenance and support. These integrators, like Yaskawa Motoman and Toshiba Machine, often work closely with the end users to design a customised automation solution that meets their needs.
Read our article about What Are Integration Costs here.
Certification organisations
In the context of the automation industry, a “cell” is a group of machines, tools, and/or robots that are used to perform a specific task or process. These cells may be located in a factory or other industrial setting and are often used to automate certain tasks in order to improve efficiency or reduce labor costs. In cases where people will be present in the same area as the cell, it is important that the cell is safety certified in order to prevent accidents or injuries. This means that the cell has been inspected and deemed safe for use by a certification organisation, which may be a government agency or a private company. These organisations may have specific guidelines or standards that must be met in order for a cell to be considered safe for use, and they may perform regular inspections to ensure that the cell continues to meet these standards.
Customers
These are the companies or organisations that actually use automation equipment in their operations. End users can be small and medium-sized businesses (SMBs) or large multinational corporations, and they use automation to improve efficiency, reduce costs, or increase productivity. End users of automation equipment and systems often have specific needs and requirements and may work with sellers, integrators, and distributors to select and implement the most appropriate automation solutions. They play a critical role in the ecosystem surrounding automation, as they are the ones who ultimately benefit from the increased efficiency and productivity that automation can provide.
Together, these players form a complex and interconnected web of technology and expertise, a living, breathing organism that is constantly adapting to meet the needs of this ever-evolving world.
We’ll remember that robotisation does sound like only one robot is involved. But it takes a village for a robot to go from being created to being fully operational on a line.
However, these players are only the tip of the iceberg, though they are the ones we will talk about most often.
Indeed, once the robot is here, another challenge this way comes for the end user, in the form of a question: Which sort of automation do I need, how will my robot operate, and how do I ensure smooth sailing the whole way through my line?
Because in the end, the ultimate goal of automation is dependable production.
Minimal issues, maximal rentability.
Part of that answer is high-sensitivity sensors, which have in recent years become a large part of the automation ecosystem. Sensors are the things we put on robots to ensure the information goes from the End of Arm Tool (EOAT) to the automation system, enabling it to function correctly. They play a crucial role in automation, as they allow the robot to sense and see its environment.
There are various types of sensors used in automation, and each one of them may be used for specific tasks. Vision sensors use light to detect and analyse visual information, such as the shape and size of objects. Location sensors determine the position and orientation of objects. Touch sensors detect physical contact and measure pressure, force, and other tactile properties. Proximity sensors detect the presence or absence of an object within a certain distance. Temperature sensors measure the temperature of an object or environment. Sound sensors detect the presence of sound or measure the intensity of sound waves.
These may be the principal ones companies use, but it is likely that we will see even more advancements in this field in the future, as technology is pushed forward and as new companies keep emerging with new and exciting systems.
We’ll remember that sensors are essentially one of the five human senses, given to a robot to improve its aim and help it feel more at home in the world. Also, so it doesn’t mess up anything and actually succeeds in its mission. Because, again, robots are not sentients and all information has to be spoon-fed to them through complex algorithms.
Challenges for the future
One of the main challenges facing the future of industrial robotics is the need to lower prices. As the number of parties involved in the production and distribution of robotics technology increases, the cost of these systems can become quite high (read: astronomical). To address this issue, solutions like robotics as a service (RaaS) are emerging, where companies can rent or lease robots instead of purchasing them outright. This allows businesses to access the benefits of robotics without the large upfront investment.
Another important challenge is maintaining high levels of reliability and safety. These are essential elements of industrial robotics, as the failure of a robot can have serious consequences in terms of both production downtime and potential risks to human workers.
Increasing flexibility is also an important challenge for the future of industrial robotics. In order to meet the needs of businesses that frequently change their production lines or product models, the technology must be able to easily adapt and be repurposed. This is particularly important for high-mix, low-volume manufacturers who may not have the volume to justify a dedicated production line for each product.
Finally, making the technology more user-friendly for non-experts is a key challenge. Currently, the programming and maintenance of industrial robots often require specialised training, which can be a barrier for companies looking to adopt the technology. Developing solutions that are easier for non-experts to use and maintain will be crucial to increasing the adoption of robotics in the manufacturing industry.
Overall, these challenges will be key considerations as the use of industrial robotics continues to grow and evolve in the coming years. However, trends such as the shift towards the use of autonomous mobile robots (AMRs) in production lines and the emergence of easy-to-use solutions from startups like Wandelbot show promising progress toward meeting these challenges and driving the future growth of the industry.
Reach out to us to discuss your automation needs.
Last news & events about inbolt
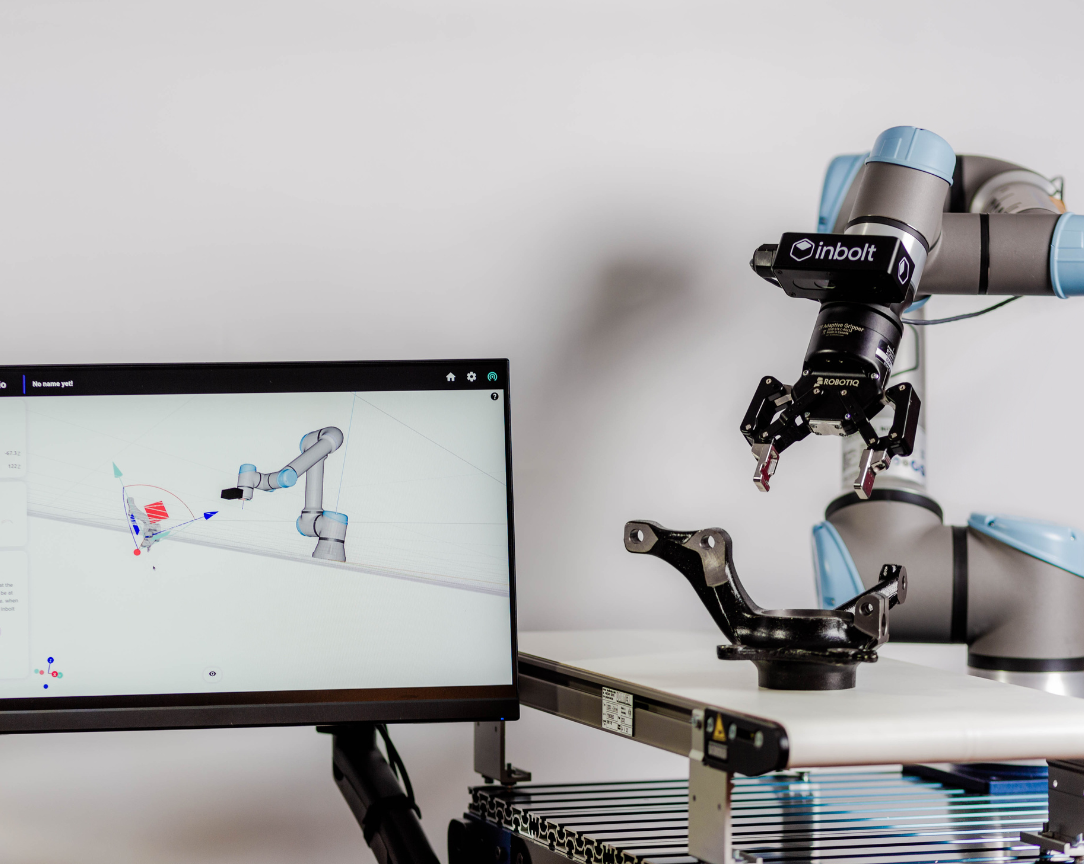
Articles
Sim2Real Gap: Why Machine Learning Hasn’t Solved Robotics Yet
The most successful areas of application for deep learning so far have been Computer Vision (CV), where it all started, and more recently, Natural Language Processing (NLP). While research in Robotics is more active than ever, the translation from research to real-world applications is still a promise, not a reality. But why?
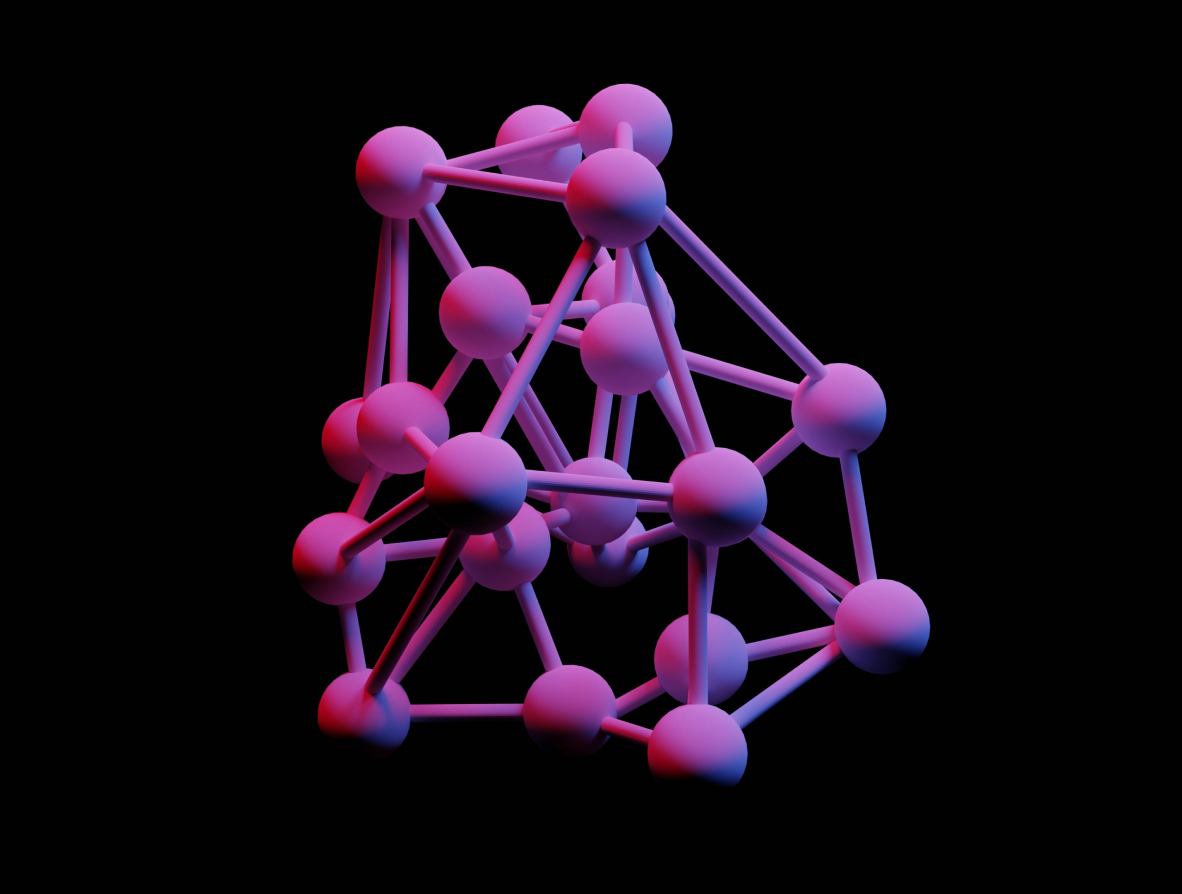
Articles
Exploring the potential of LLMs in robotics: an interview with Louis Dumas
Robotics has always been at the forefront of technological advancement, but translating human ideas into robotic actions remains one of its greatest challenges. In an interview with Louis Dumas, co-founder and CTO of inbolt, he shared his insights into the transformative potential and current limitations of Large Language Models (LLMs) in the robotics field.