Robotic picking & End Effectors
Automated bin picking is the process where AI-controlled machines manipulate a pick and place arm to retrieve products from a bin. This technology relies on the integration of robotics and computer vision.
Before robotic bin picking, there was pick and place.
Traditional bin picking was based on 2D vision systems, where robots followed predefined trajectories. This method, known as pick and place, has a long history in automation.
Pick and place
Pick and place robots are mechanical arms programmed by software to grab components and place them elsewhere with precision. This technology began in the 1980s and has steadily improved with advancements in technology.
These machines don’t require extensive training. Instead, a new function can be taught by uploading the necessary program.
Pick and place technology relies on software that pre-programs the machine to build a particular product. While these devices are not AI-driven and cannot learn or adjust their processes autonomously, they can be reprogrammed to assemble various types of products. Their programming can be adjusted to teach new methods.
The primary characteristics of pick & place include:
- Fixed Trajectories: The robot follows predefined paths to pick and place items.
- Known Positions: The locations of the items to be picked and where they will be placed are known and unchanging.
- Repetitive Tasks: Often used for repetitive tasks where the same motion is repeated consistently.
Bin picking
Automated bin picking is the process where AI-controlled machines manipulate a pick and place arm to retrieve products from a bin. This technology relies on the integration of robotics and computer vision.
While both pick and place and bin picking involve relocating items, pick and place operates in a structured environment with known positions. In contrast, bin picking manages randomly placed items in an unstructured environment.
The primary characteristics of bin picking include:
- Randomized Item Placement: Items are not in fixed positions and can be oriented in any manner within the bin.
- Autonomous Path Planning: The robot must autonomously plan its path to pick up an item without disturbing other items.
- Dynamic Environment: The robot must adapt to a constantly changing environment where the positions and orientations of items are variable.
The camera will align the model of the component it was fed, and will recognise it in real life. It will then calculate the trajectory, optimize the journey, and pick the item from the bin before putting it in its rightful place without damaging the component. It will then keep going until the camera can no longer recognise any more items in the bin.
The machine relies on a 3D camera that scans the container to interpret an image like a human eye so that the robot can grab a particular item from the bin.
It all sounds really simple, but it is in fact a feat of modern technology, and for cause: it involves the picking of overlapping complex objects that have an undefined position, and subsequent grasping and placing.
Here are all the difficulties :
- Random Order Grasping: Components must often be grasped in a random order.
- Object Recognition Failures: Components may not be recognised due to reflections, shininess, or lighting conditions, which depend on the vision sensor technology and the resolution of the 3D map.
- Pose Estimation Failures: An item may be recognised, but an inaccurate 3D pose estimation can lead to a failed grasp.
- Robot Motion Constraints: Robots have inherent blind spots and areas they avoid to prevent self-damage, akin to a coded "survival instinct."
Advantages and Benefits of Bin Picking in the Manufacturing Industry
A bin picking system can operate without a 3D vision system, especially in simple applications where the items to be picked have a relatively uniform shape and size, and their orientation doesn’t vary significantly. This is also feasible if the environment has consistent lighting and minimal occlusions, and if the robot’s task does not require depth information.
However, in any other case, a bin picking system will enhance the ability to locate, position, and orient parts effectively. It often boasts a 3D vision system, and will usually includes a robotic arm integrated with the vision system.
That being said, it will still be missing one of the main elements: the end-effector.
Choosing the Right End-Effector for Bin Picking
All robots are sold without the end effector (End-Of-Arm-Tooling), as each mission requires a different end effector, most of which are often custom-built for specific tasks.
Without an end effector, a robot is unable to perform any operations.
In the manufacturing industry, there are hundreds of types of end effectors, and numerous companies specialize in making them, including grippers, process tools, sensors, and more. The main ones are going to be grippers, which are primarily used to hold and move components accurately. These components can vary greatly in complexity and weight. As a result, there are many styles and sizes of grippers, including two-finger to multiple-finger grippers, suction grippers, magnetic grippers, soft grippers, and more, used for material handling, assembly, sorting, etc.
End effectors can be sourced from robot manufacturers, third-party component manufacturers, integrators, and specialty shops. For specific applications, you may need to contact a third-party supplier or integrator.
The cost of end effectors varies widely based on their type and complexity. Small pneumatic grippers or suction cup systems can cost a few hundred USD, while more complex or specialized grippers, or large systems, can cost several thousand dollars. High-end systems such as powerful electromagnets, welding systems, or advanced vision systems can reach into the tens of thousands of dollars (USD).
The evolution from traditional pick and place systems to advanced bin picking technologies marks a significant milestone in manufacturing automation. Traditional pick and place robots, with their predefined trajectories and known positions, laid the foundation for modern automation. However, the advent of bin picking, driven by the integration of AI, robotics, and computer vision, has revolutionized the industry by enabling robots to operate in unstructured environments with randomly placed items.
The implementation of 3D vision systems and sophisticated end effectors has expanded the capabilities of robotic systems, making them even more adaptable, precise, and efficient.
As technology continues to advance, we can expect further innovations in robotic picking systems, driving the future of manufacturing automation forward.
Last news & events about inbolt
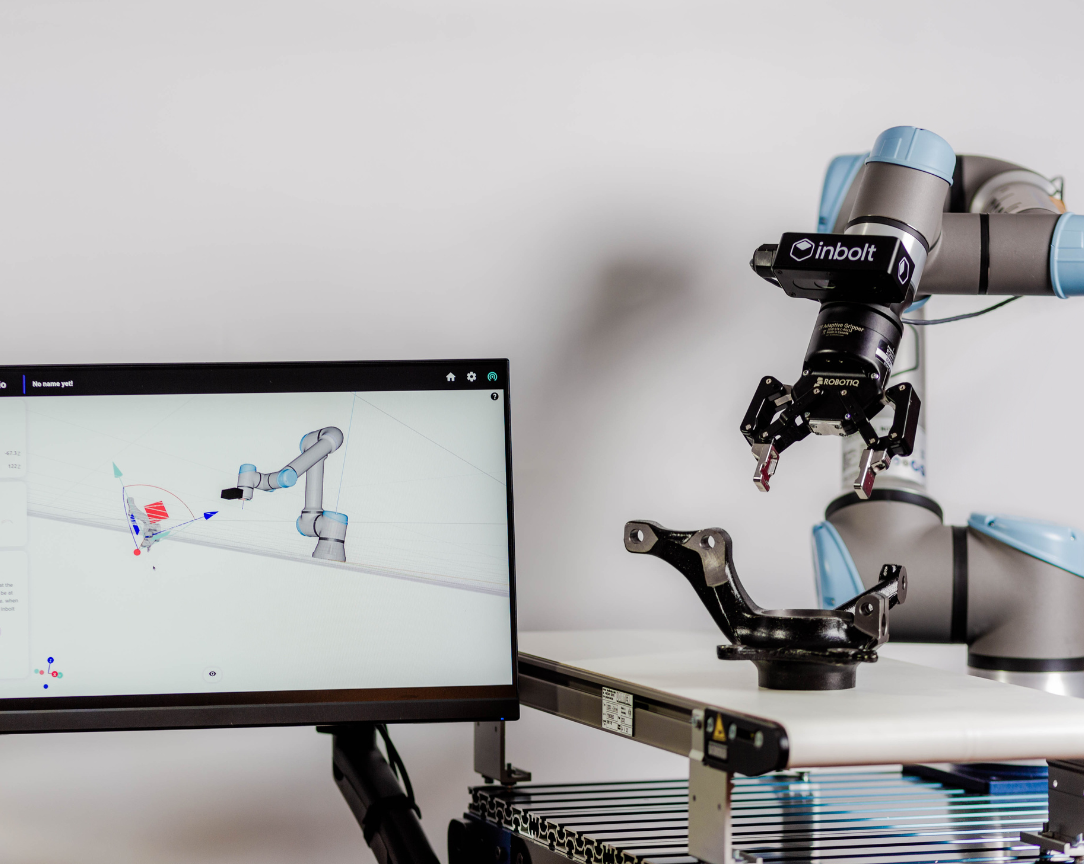
Articles
Sim2Real Gap: Why Machine Learning Hasn’t Solved Robotics Yet
The most successful areas of application for deep learning so far have been Computer Vision (CV), where it all started, and more recently, Natural Language Processing (NLP). While research in Robotics is more active than ever, the translation from research to real-world applications is still a promise, not a reality. But why?
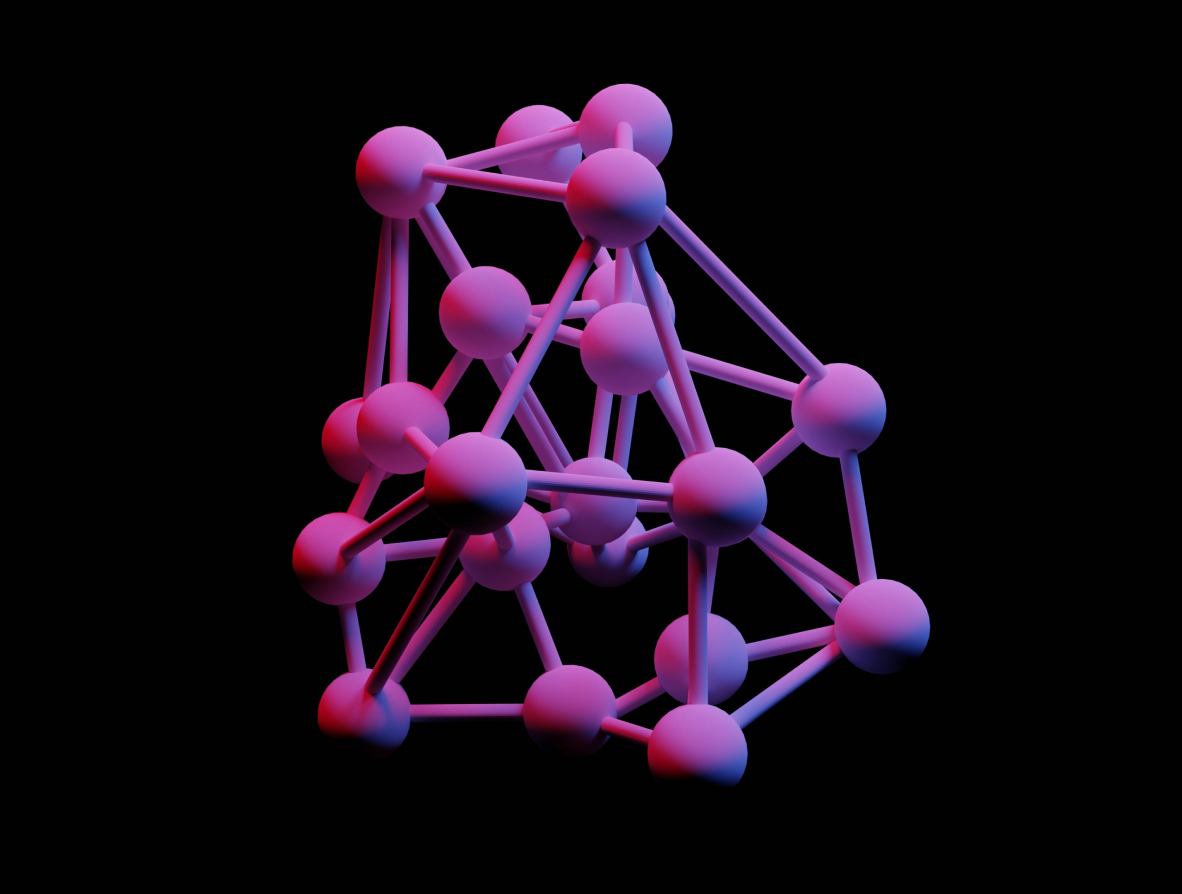
Articles
Exploring the potential of LLMs in robotics: an interview with Louis Dumas
Robotics has always been at the forefront of technological advancement, but translating human ideas into robotic actions remains one of its greatest challenges. In an interview with Louis Dumas, co-founder and CTO of inbolt, he shared his insights into the transformative potential and current limitations of Large Language Models (LLMs) in the robotics field.