‘Precision’ vs. ‘Accuracy’ in Robotics
When giving a robot arm a task, you want the robot to be accurate, which means it should go exactly where you tell it to. Unfortunately, even if the robot can consistently move to the same spot over and over again (repeatability), it might not be exactly where you wanted it to be in the first place.This difference is what we call inaccuracy.
“In robotics, positioning accuracy is the error between the requested point to reach and the measured position actually reached by the robot. Precision, more commonly referred as repeatability, is the robot’ ability to consistently reach the same given position.”
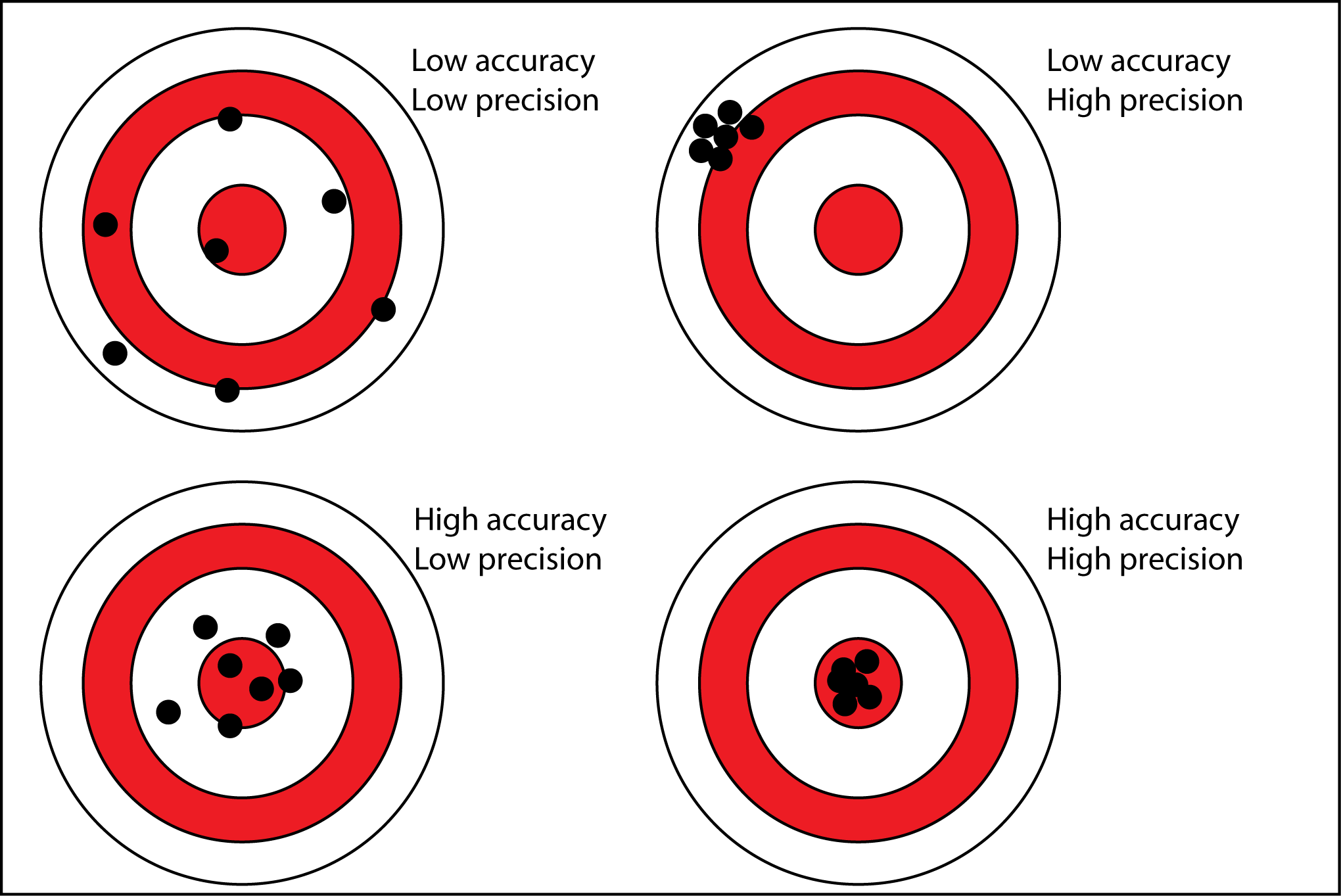
Definition & difference
Why are Robots Inaccurate?
When giving a robot arm a task, you want the robot to be accurate, which means it should go exactly where you tell it to. Unfortunately, even if the robot can consistently move to the same spot over and over again (repeatability), it might not be exactly where you wanted it to be in the first place.
This difference is what we call inaccuracy.
There are a few reasons why robots might not be completely accurate:
- Manufacturing and Assembly Differences: The robot might not be built and put together perfectly. The parts might be mildly different sizes or shapes than what was planned.
- Robot's Own Weight and What It's Holding: The parts of the robot can bend or stretch a little under their own weight, or the weight of whatever the robot is carrying.
- Temperature Changes: Parts of the robot can expand or contract with changes in temperature.
These small changes in size can affect where the robot moves, so even though the robot is trying to move to the right spot (and thinks it is), these factors can cause it to be a little off.

Do you Really Need Accuracy?
Although most industrial robots are highly repeatable, they often lack accuracy.
This is not necessarily an issue when the robot is used for simple repetitive tasks, where the points to be reached can be known in advance.
For example, if a task only requires moving from point A to point B, and then back to point A, both points could be taught manually (i.e., the operator would guide the robot towards its desired position using a handheld robot programming device called a teach pendant, and save its corresponding joint positions): As the robot is repeatable, it would be able to reach those points again and again with a low random error rate, and the task would be completed successfully.
However, high repeatability alone is no longer enough when the points to be reached cannot be memorized in advance, as is the case in the following situations:
- The points to be reached are transmitted to the robot in real time by an external device, for instance a camera, detecting parts to be gripped.
- A task involves a large number of points—such as drilling thousands of holes on a surface—and manually teaching them would be tedious.
Since the positioning error of industrial robots can sometimes exceed 1mm, some tasks could be compromised by this lack of accuracy.
How to Improve a Robot’s Accuracy?
A robot is, for all intents and purposes, a puppet on strings. You want to control it precisely, but sometimes the puppet doesn't move exactly how you want. Calibration is like this: fine-tuning the strings and the puppet's movements to make them more precise.
- Understanding the Robot's Structure with DH Convention: The Denavit-Hartenberg (DH) convention is a detailed guidebook for the robot's movements. It helps in understanding how each part of the robot is connected, and how it moves in relation to the other parts.
- Kinematic Calibration: Kinematic calibration involves adjusting the robot's movement instructions (DH parameters) based on real measurements (like using a laser to track where the robot's hand actually goes).
- Local Calibration: If a robot only needs to be extremely precise in a certain area, you can focus the calibration just on that area to make it easier to calibrate.
- Non-Kinematic Calibration: Non-kinematic calibration looks at all the other factors affecting the robot's movements, like how stiff the joints are (joint compliance), how much play is in the gears (gear backlash), or how temperature affects the materials.
- Model-Free Approaches: Model-free approaches allows the engineers to observe where the robot tends to make errors, and then adjusting its movements to compensate, without worrying too much about the underlying reasons for those errors.
So, in simple words, calibration is about fine-tuning and correcting the robot's movements in various detailed ways to make it perform its tasks as accurately as possible.
Can Vision-Guided Robotics Improve the Robot’s Accuracy?
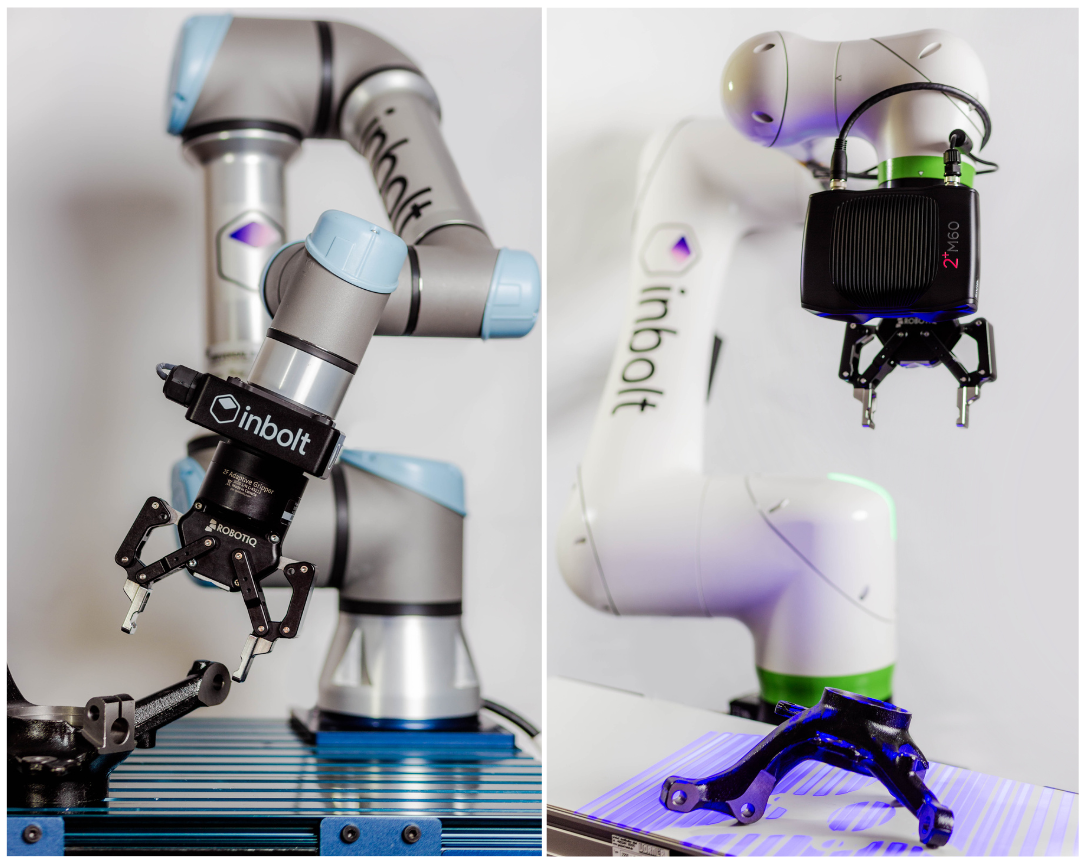
Vision-based robot servo control overrides the robot’s potential accuracy issues.
It makes the robot more precise, but for it to work well, two things are important: the 'eyes' must see clearly, and they must be perfectly in sync with the 'brain'. If both are spot-on, the robot can move exactly where it should.
Vision systems can help compensate for the accuracy limitations of industrial robots through:
- Visual Feedback: Provide real-time visual feedback to the robot, allowing it to adjust its position and orientation during a task.
- Realign: Update the robot's actual position and orientation, relative to the workpiece, before and during a task. This allows adjustments to be made on the fly.
- Object Detection: Identify objects, their locations, and orientations, enabling the robot to adapt its movements where objects may not be perfectly aligned or positioned.
- Path Planning and Collision Avoidance: Help the robot plan its path to avoid obstacles and potential collisions, ensuring safe and accurate movement in dynamic environments.
- Adaptive Control: Most vision-guided robots (particularly 3D vision) can adapt to variations in the environment (changes in lighting conditions for example), to maintain accuracy and reliability.
These techniques fine-tune a robot's movements and account for several factors, from its physical structure to the environment's influence.
However to really improve a robot’s accuracy based on vision, the accuracy required for the hand-eye calibration takes a whole new dimension. Stay tuned for an upcoming article!
Inbolt’s Advantage
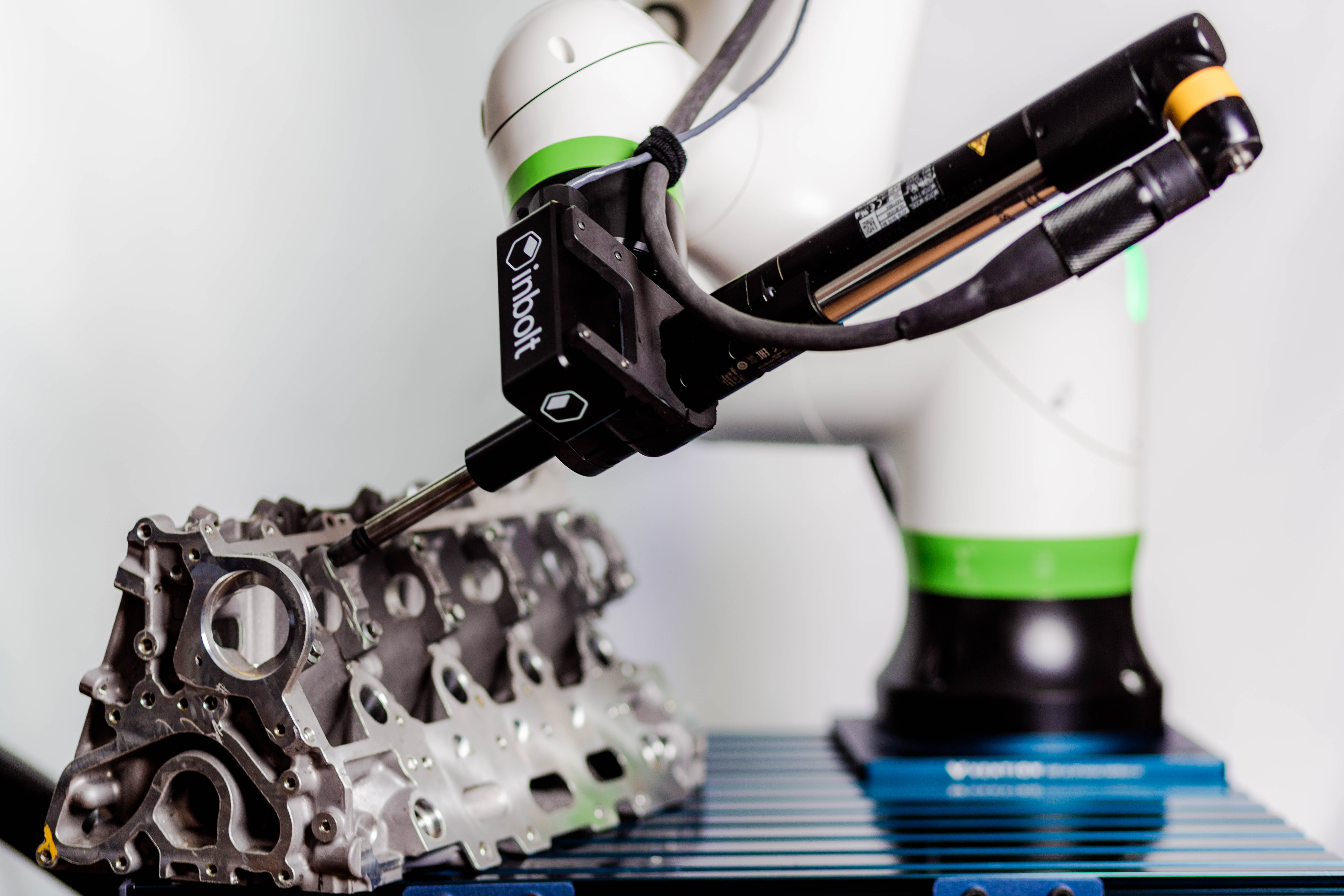
What we do at Inbolt takes this a step further. By integrating advanced 3D vision with real-time servo-control and the cutting-edge AI of Inbrain, Inbolt strives to be both extremely precise and efficient. GuideNOW is capable of processing large amounts of 3D data, adapting the robot's trajectory in real-time to ensure the precise and efficient mission of the robot’s task on the workpiece placement.
With a specific focus on its 80ms response time and powered by 3D modeling and AI, Inbolt’s core technology takes on a workpiece-centric approach with real-time decision-making capabilities. This ensures that the solution is reliant on 3D scans and models, yet remains independent of environmental constraints or the need for markers.
Reach out to us to learn more about how you can automate your automation process.
Last news & events about inbolt
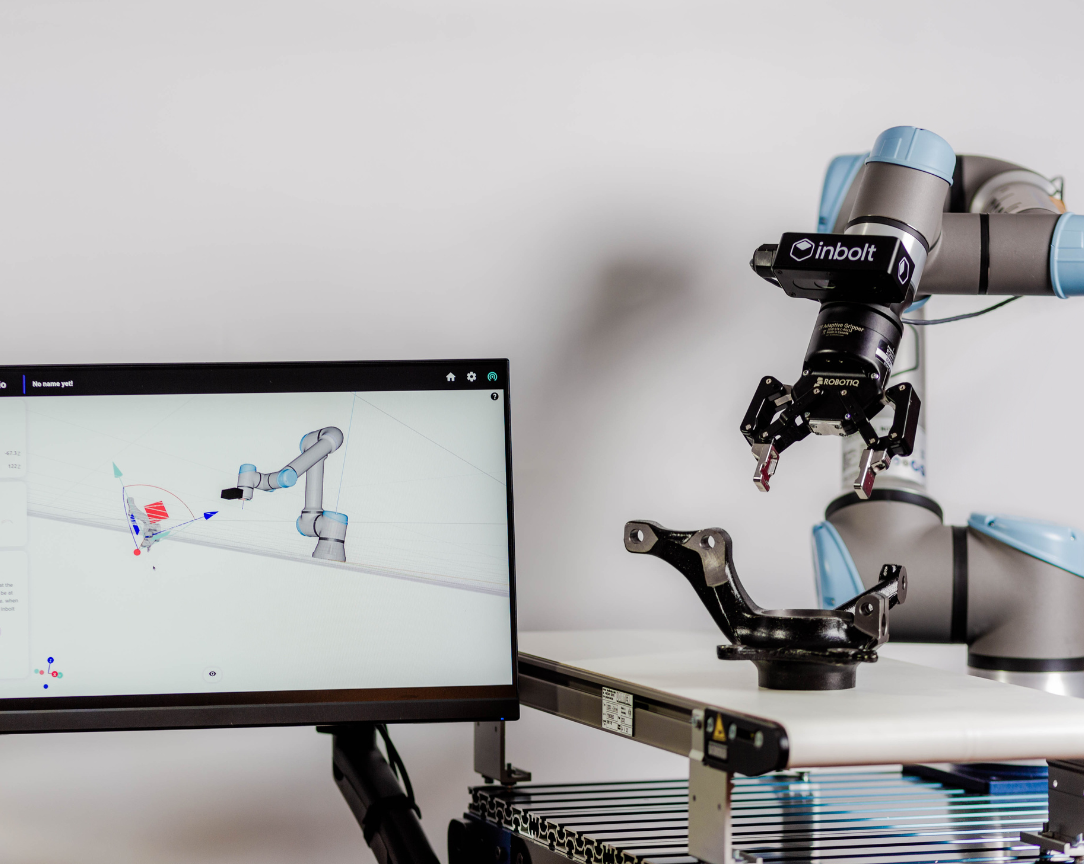
Articles
Sim2Real Gap: Why Machine Learning Hasn’t Solved Robotics Yet
The most successful areas of application for deep learning so far have been Computer Vision (CV), where it all started, and more recently, Natural Language Processing (NLP). While research in Robotics is more active than ever, the translation from research to real-world applications is still a promise, not a reality. But why?
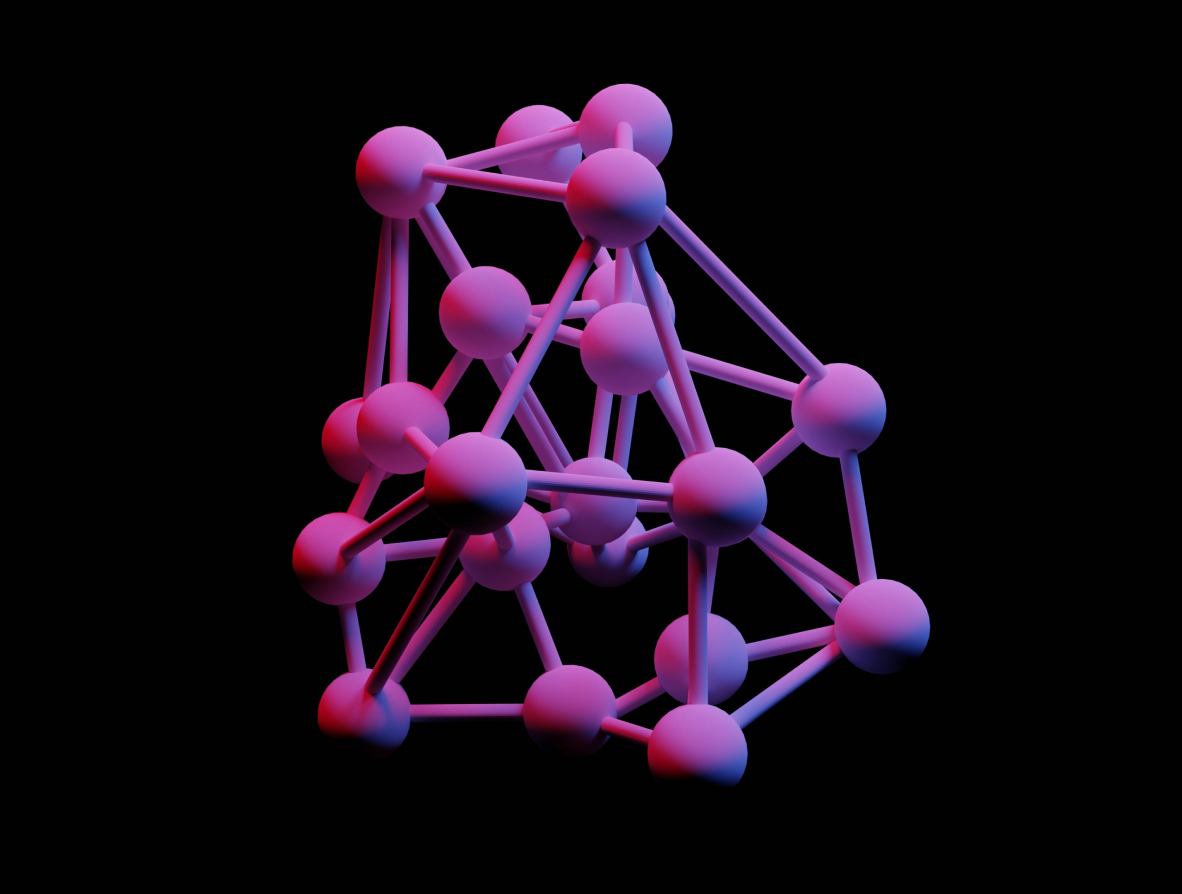
Articles
Exploring the potential of LLMs in robotics: an interview with Louis Dumas
Robotics has always been at the forefront of technological advancement, but translating human ideas into robotic actions remains one of its greatest challenges. In an interview with Louis Dumas, co-founder and CTO of inbolt, he shared his insights into the transformative potential and current limitations of Large Language Models (LLMs) in the robotics field.