Optimizing Automation Costs with Vision-Based Robot Guidance
From highly constrained environments to vision-guided robotics, the world of automation is constantly evolving. Discover how the paradigm shift towards vision-guided robotics is changing the game and why manufacturers must embrace it to stay competitive.
The world of robotics has experienced tremendous growth over the past few decades, with industrial robots playing a crucial role in modern manufacturing processes. And yet, despite significant advancements in robotics technology, many industrialists still have limited knowledge of vision-based robot guidance systems.
The aim is to introduce these systems and discuss the advantages of vision-based guidance over traditional constrained environments.
Understanding Constrained Environments
A constrained environment refers to the physical limitations and boundaries imposed on a manufacturing process, typically through the use of jigs or fixtures.
đź’ˇ We recently released an article with more in-depth information covering this topic.
These constraints help ensure that the robot performs its tasks accurately and consistently in the correct position. However, these constraint environments can also limit flexibility, increase costs, and make it challenging to adapt to new manufacturing processes. Indeed, every time a new process is engaged, the constraints have to be recreated over the entirety of the line.
From Highly Constrained to Flexible Environments
Jigs and Fixtures
Jigs and fixtures are mechanical devices used to hold and position parts during a manufacturing process. They provide a highly constrained environment to ensure accuracy and repeatability but can be expensive and time-consuming to produce and store. They are not easily adaptable to changes in product design, making them less flexible compared to vision-based guidance systems. Industrials have been trying to find ways to get rid of them for years, with various levels of success.
In the automotive industry, Nissan figured out a way to 3D print some of the fixtures needed for their needs, while BMW worked on fixing the problem at the source with fixtureless assembly that relies on inherent mate and fastening features on sheet-metal parts.
Markers and 2D Vision
Markers and 2D vision systems offer a less constrained environment compared to jigs and fixtures. These systems use cameras to detect markers placed on objects or the manufacturing environment, allowing the robot to determine its position relative to the object. While this approach reduces the reliance on mechanical constraints, it still requires some level of fixturing to maintain accuracy and can struggle with occlusion and varying lighting conditions amongst other things.
Triangulation-based technologies
Triangulation-based technologies, like ultra-wideband (UWB), infrared, or ultrasound, are commonly used in robotic automation systems to help the robot move based on the location of certain points on the workpiece. To do this, beacons are placed around the line, trackers are attached to the robot and the workpiece, and triangulation is used to determine the workpiece's position in relation to the robot's end effector.
Setting up these systems can be complex and time-consuming, as they require precise calibration between the robot trackers and the TCP or tracker workpiece and can suffer from accuracy issues (if the tracker is moved or obscured by an object, it can result in errors in the robot's movements). They’re also generally very expensive, making it unsuitable for smaller businesses. Additionally, these systems do not entirely remove the issue of flexibility, as workpieces still require jigs to be indexed in the same way on the trolley with the tracker.
Despite these limitations, companies such as Humatics continue to develop and improve triangulation-based technologies for robotic automation systems, allowing companies to benefit from increased precision and reduced downtime in the specific cases triangulation can be applied to.
3D Vision and Triangulation
3D vision systems represent the next step in reducing the constraints in a manufacturing environment. Using techniques like triangulation, structured light, or time-of-flight, these systems can generate a 3D representation of a workpiece or a specific environment. This allows for more accurate object recognition, pose estimation, and guidance for the robot, even in environments that wouldn’t work otherwise, like dark factories.
By reducing the reliance on mechanical constraints, 3D vision systems offer greater flexibility and adaptability in the manufacturing process, making them an ideal choice for industries that require frequent changes in product design, such as companies with high mix and low volume needs which have seen a steady rise in the past ten years with the advent of mass product customisation, as a response to the increasing demand from customers, willing to pay up to 20% more for the opportunity to have a personalized experience.
inbolt and GuideNOW
We at inbolt have developed an innovative vision-based robot guidance solution called GuideNOW. By leveraging advanced 3D vision and artificial intelligence, the GuideNOW system provides an intuitive and efficient way to guide industrial robots, reducing the need for mechanical constraints and significantly improving manufacturing flexibility.
The GuideNOW system uses a combination of cameras and advanced algorithms to recognise and track objects in real-time, enabling robots to adapt to changes in object position, orientation, or shape. This eliminates the need for costly and time-consuming jigs and fixtures, leading to lower production costs, shorter lead times, and increased adaptability to new product designs.
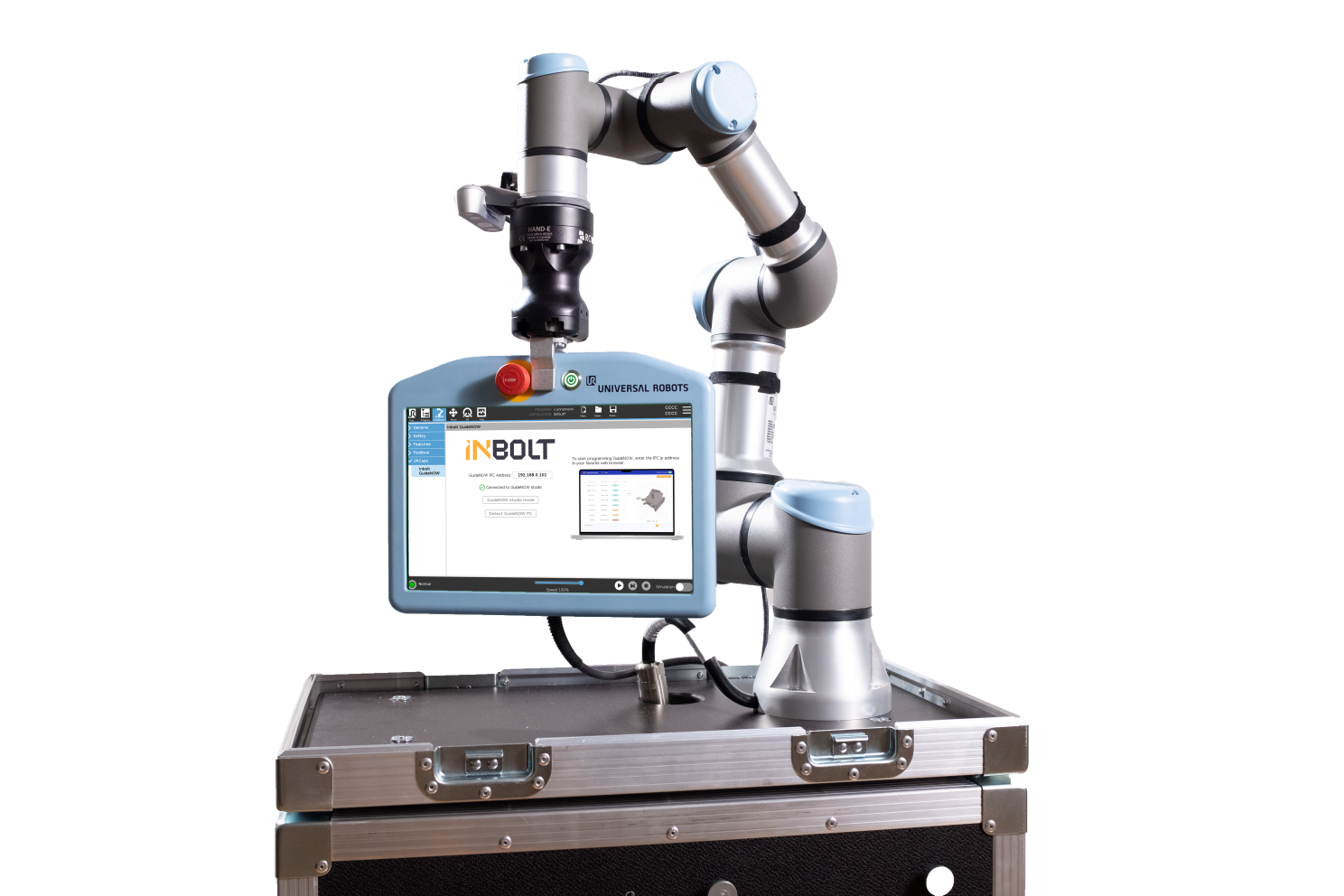
Automation is one of these things that gets greatly impacted by new technologies, and it can be quite difficult to keep one’s head over the water and remember to keep in touch with the new opportunities being created and remain informed, especially when it comes to new technologies that could positively impact the automation chain.
By embracing the paradigm shift towards vision-guided robotics and slowly moving away from highly constrained environments that rely on jigs and fixtures, manufacturers can stay ahead of the competition and ensure the long-term success of their businesses.
In France, this process is being encouraged by the government with their “Made in France” plan included in France 2030, and might lead to more requests for automation systems and line improvements.
Reach out to us to discuss your automation needs.
‍
Last news & events about inbolt
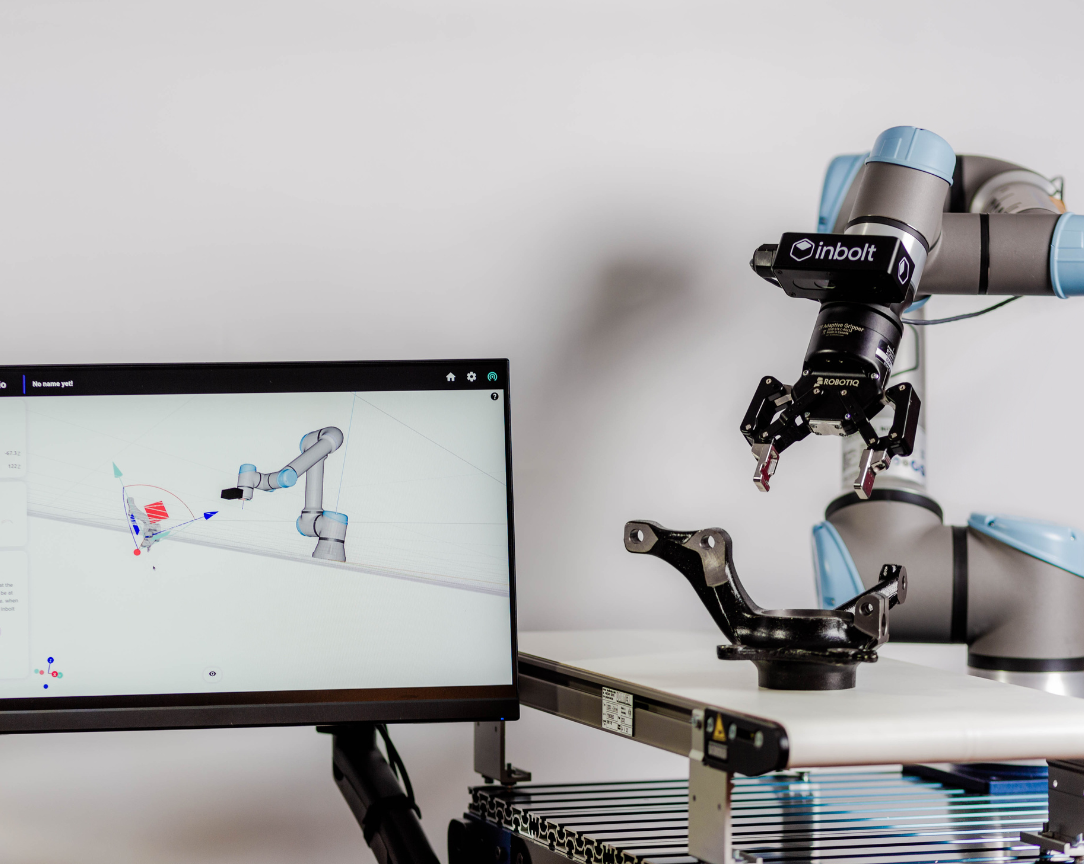
Articles
Sim2Real Gap: Why Machine Learning Hasn’t Solved Robotics Yet
The most successful areas of application for deep learning so far have been Computer Vision (CV), where it all started, and more recently, Natural Language Processing (NLP). While research in Robotics is more active than ever, the translation from research to real-world applications is still a promise, not a reality. But why?
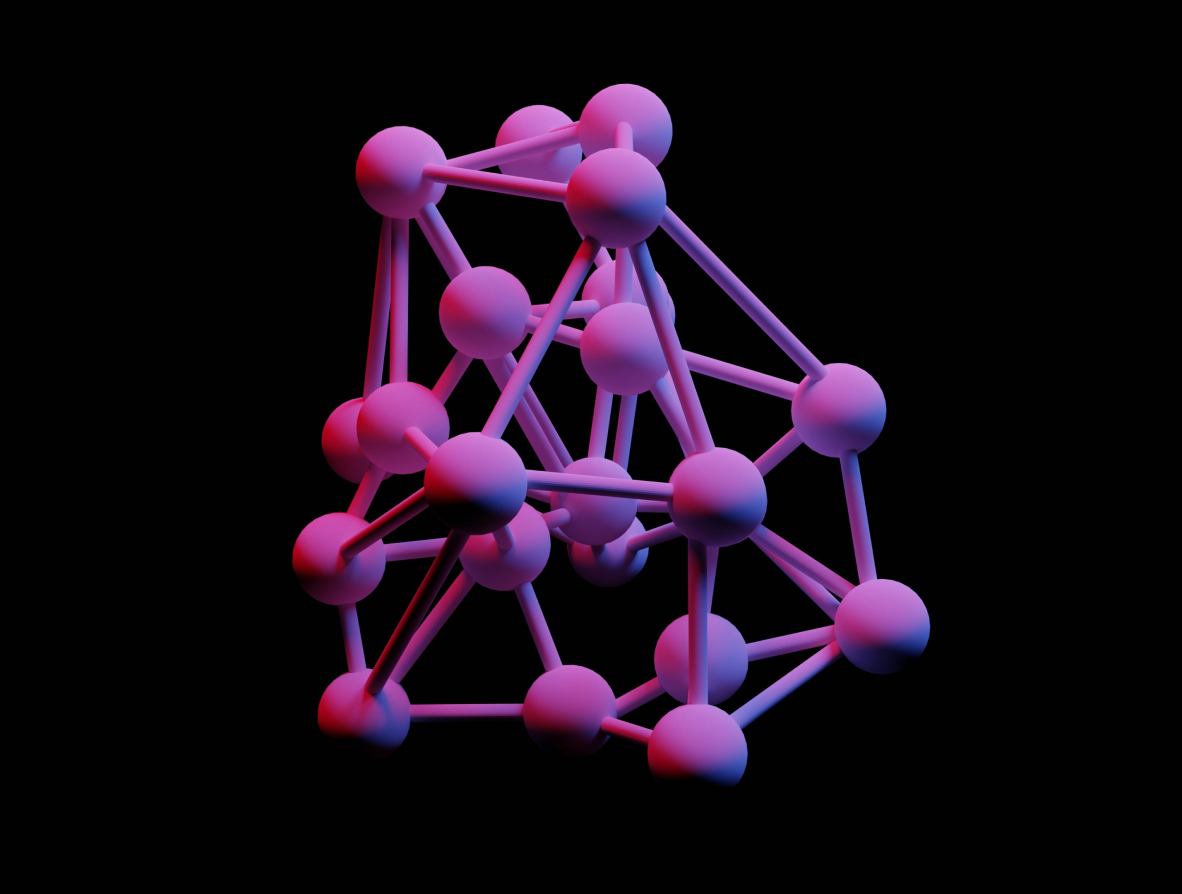
Articles
Exploring the potential of LLMs in robotics: an interview with Louis Dumas
Robotics has always been at the forefront of technological advancement, but translating human ideas into robotic actions remains one of its greatest challenges. In an interview with Louis Dumas, co-founder and CTO of inbolt, he shared his insights into the transformative potential and current limitations of Large Language Models (LLMs) in the robotics field.