Industrial robots vs cobots
Industrial robots have dominated the automation of industries for decades. Cobots, on the other hand, really started to take off in 2008. So, what is the difference between the two?
Industrial robots have dominated the automation of industries for decades (since the 1950s, in fact). Cobots, on the other hand, were first introduced in 1996 but really started to take off in 2008 with Universal Robots and the release of the UR5.
(A cobot is) a device and method for direct physical interaction between a person and a computer-controlled manipulator.
J. Edward Colgate and Michael Peshkin, inventors of the first cobot
Since their rise to fame in the early 2000s, cobots have only grown in popularity; they can be found in many different industries, from pharmaceuticals to automobiles, working next to humans…and next to industrial robots.
So, what’s the difference between the two?
But first, a quick lesson Degrees of Freedom (DoF).
Degrees of Freedom
A robot will always have a certain degrees of Freedom (DoF), which is a way of saying how freely and in how many ways a robot can move. More degrees of freedom mean the robot can do more complex movements and can work in tight spaces, but these are also more expensive and complicated to program.
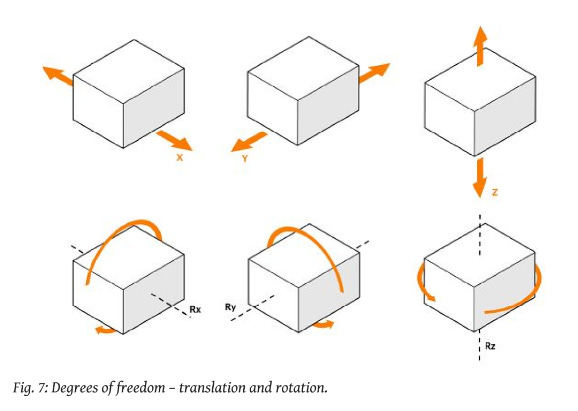
One axis: Simple linear or rotational movement, for limited tasks (up/down, forward/backward, or side to side).
Two axes: Move in two directions, without tilting or rotating the held object.
Three axes: Move to any point within its reach without tilting or rotating the object it’s holding.
Four axes: Adds the ability to rotate the object, like a wrist rotation in one plane.
Five axes: Allows the robot to approach objects from different angles and rotate them in two planes.
Six axes: Total freedom – it can move anywhere and rotate in any direction. Six degrees of freedom are usually enough for most tasks a robot needs to do (assembly, heavy lifting). If a robot has fewer, it's often specialized for simpler tasks.
Seven axes: Like 6, but offers more sophisticated movement options, enhancing the ability to maneuver around obstacles without moving the payload.
Both industrial robots and cobots will have degrees of Freedom that are the same, regardless of the type of robot.
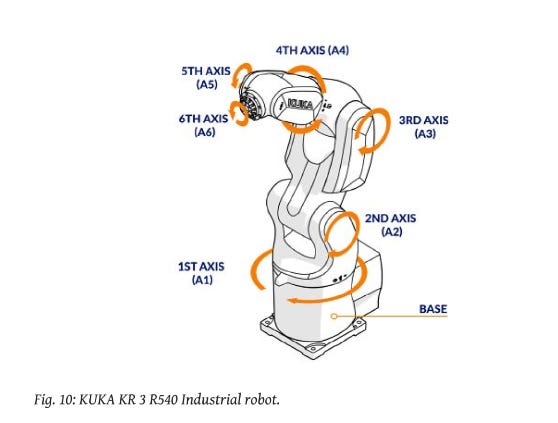
Uses, Design & Safety Mechanisms of an Industrial Robot
Invented several decades before cobots, industrial robots have been engineered and optimized for autonomous operations in repetitive, precise, and/or hazardous tasks. An industrial robot is a robot built on several axes, programmed to execute a specified action with remarkable consistency, speed, and little to no need for human intervention.
As their first purpose is to replace humans, and not work alongside them, they were designed to operate in isolated environments; human interaction is therefore minimal to ensure safety. Each industrial robot functions within designated zones, often separated by barriers or cages. While they are all equipped with emergency stop mechanisms, these robots are not intrinsically capable of detecting humans, and thus, incapable of responding to their potentially dangerous presence.
Once programmed, these robots are incredibly useful; however, the initial programming and subsequent reconfigurations demand considerable time and expertise. Each modification demands a thorough reprogramming, which can only be undertaken by professionals in the field.
Appearance of an industrial robot
- Mechanical Unit & Motors: The parts that move. Like human arms, the mechanical unit and motors are the robot's joints and muscles that help it move.
- Control Cabinet: The brain of the robot. It tells the robot what to do and when to do it, based on the programming it receives.
- Teach Pendant/Operator Panel: The device that humans use to teach the robot, or give it specific commands.
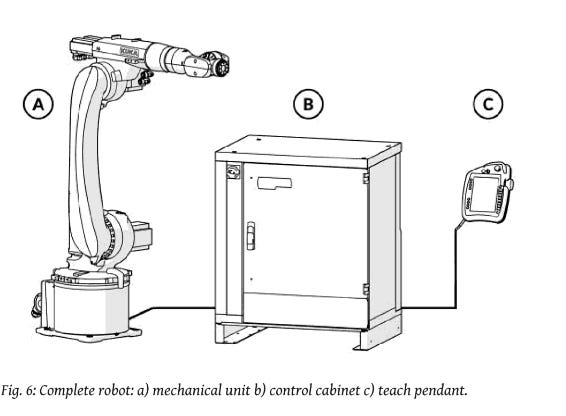
Application & Industry Reach of an Industrial Robot
- Suitable for a variety of tasks requiring human-robot interaction, such as assembly, inspection, and packaging.
Key Considerations for the Selection of an Industrial Robot
- When to Choose: Ideal for environments requiring frequent human interaction, flexibility, and adaptability.
- Key Benefits: Enhanced safety, ease of integration, and user-friendly interfaces.
Industrial robots essentially are the ultimate programmable mechanical arms, that can help make or move almost anything in factories. An industrial robot is designed for high-speed, high-precision repetitive tasks in isolated environments, and thus comes with a hefty price tag…but also happens to last for years. They were created for the automotive industry, to work on a specific reference for years, doing the same thing.
What is a Collaborative Robot (cobot)?
In contrast to the autonomously operating industrial robots, a collaborative robot is designed to work alongside human operators within a shared workspace. Its role is to help with human tasks, rather than replacing humans entirely. Cobots are built to be inherently safe and interactive, allowing close human-robot collaboration without the need for physical barriers or safety cages.
Cobots are typically more user-friendly and require less specialized knowledge to program, compared to traditional industrial robots. They can be programmed through more intuitive methods, like hand-guiding, or by using simple graphical interfaces, allowing non-expert staff to reconfigure them for different tasks with minimal downtime.
While their payload and speed are generally lower than those of industrial robots, making them unsuitable for some high-speed, high-load applications, cobots excel in tasks that benefit from human-robot collaboration, such as lightweight assembly, packaging, tightening, glue application, etc.
Appearance of a cobot
- Mechanical Unit & Motors: They have joints and actuators (motors) enabling motion, typically designed to be safer and more adaptable to work alongside humans.
- Control System: This serves as the cobot's brain. Cobots often feature more advanced sensors and AI to safely interact with human workers, adjusting their actions in real-time.
- Interface or Operator Panel: Unlike the teach pendants of traditional robots, cobot interfaces are usually more intuitive.
Uses, Design & Safety Mechanisms of a cobot
- Flexible and efficient, they were engineered to be collaborative by nature.
- There is no need for cages and security constraints, as advanced sensors are implanted directly into the robot to allow them to coexist safely alongside humans (force and torque sensors designed to halt or modify operations upon detecting human presence). They can be operated in shared spaces, in direct interaction with humans.
- Easy to use, they are easily reprogrammable and adaptable to a lot of tasks without significant reconfiguration.
Application & Industry Reach of a cobot
- Predominantly manufacturing but also found in automotive, electronics, and heavy industries. Ideal for high-precision, high-speed, or hazardous tasks that are beyond human capability.
Key Considerations for the Selection of a cobot
- When to Choose: Best suited for tasks that demand speed, and precision, and can be delineated from human activities.
- Key Benefits: High efficiency, reliability, and capability to handle dangerous tasks.
Cobots are built to work alongside humans, assisting without compromising safety. Their design allows direct interaction and collaboration, with built-in safety features like force sensors and soft padding to prevent injuries. They are versatile tools that enhance human capabilities, especially in tasks requiring precision or repetitive motion.
How do I choose between a cobot and an industrial robot for my use case?
To chose the best option for your use case, you must understand the type of automation process that’s needed for your activity, and, as such: What is the degree of human-robot interaction your operations necessitate? While cobots excel in environments requiring close human collaboration, industrial robots are better suited for tasks demanding minimal human intervention. What is the level of precision and speed your tasks require? The spatial constraints of your available workspace also play a decisive role, as does your budget.
There has been a lot of talk of cobots replacing humans, but this isn’t what cobots were made for. Cobots aren’t even made to replace industrial robots. There are specific tasks that industrial robots are better equipped for, just as there are specific tasks that cobots — or humans — are better equipped for.
Either way, one thing’s for sure: industrial or cobot, your robot needs eyes. Reach out to determine if your current processes could benefit from inbolt’s technology.
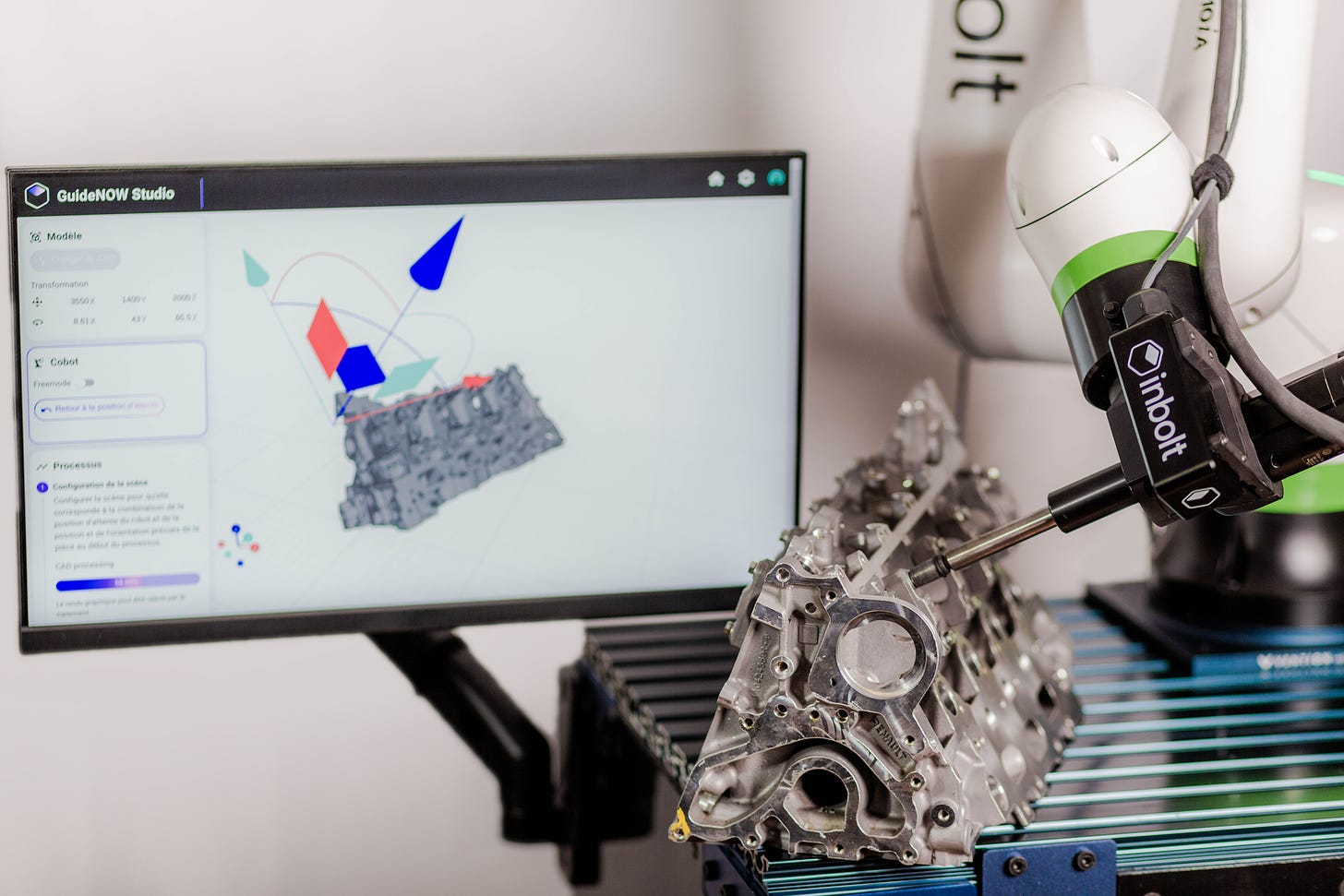
Last news & events about inbolt
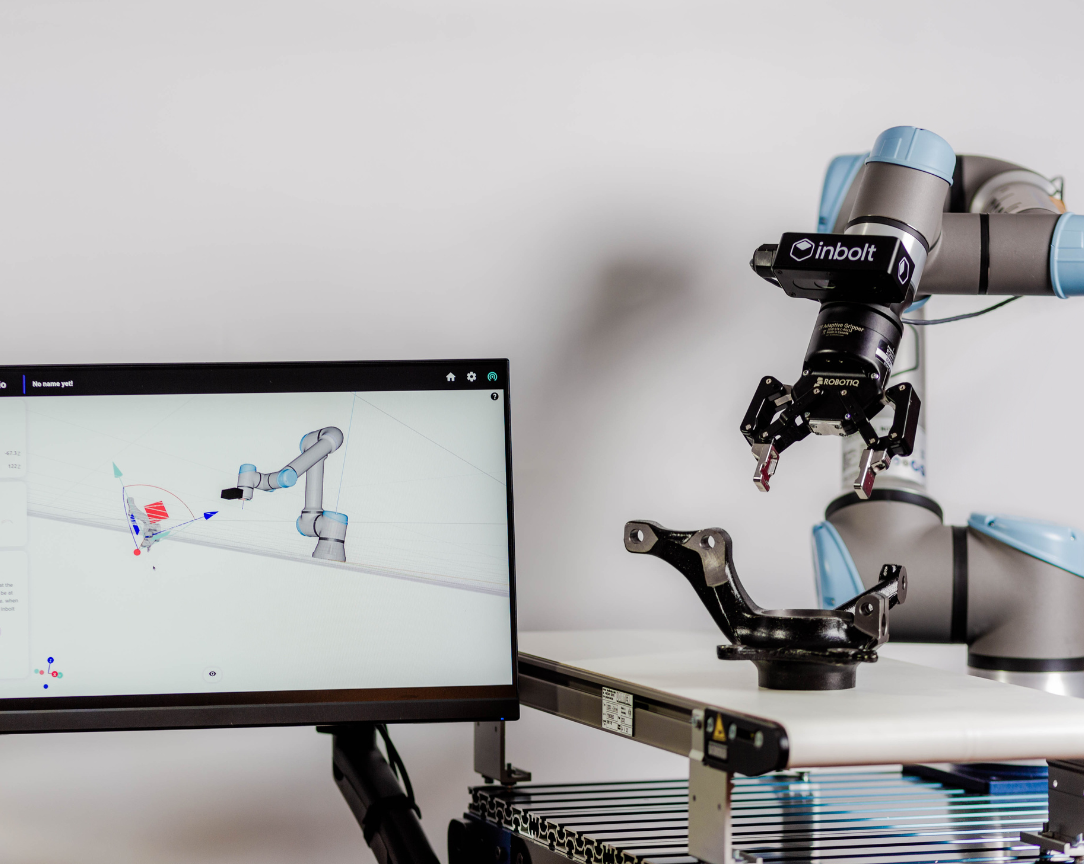
Articles
Sim2Real Gap: Why Machine Learning Hasn’t Solved Robotics Yet
The most successful areas of application for deep learning so far have been Computer Vision (CV), where it all started, and more recently, Natural Language Processing (NLP). While research in Robotics is more active than ever, the translation from research to real-world applications is still a promise, not a reality. But why?
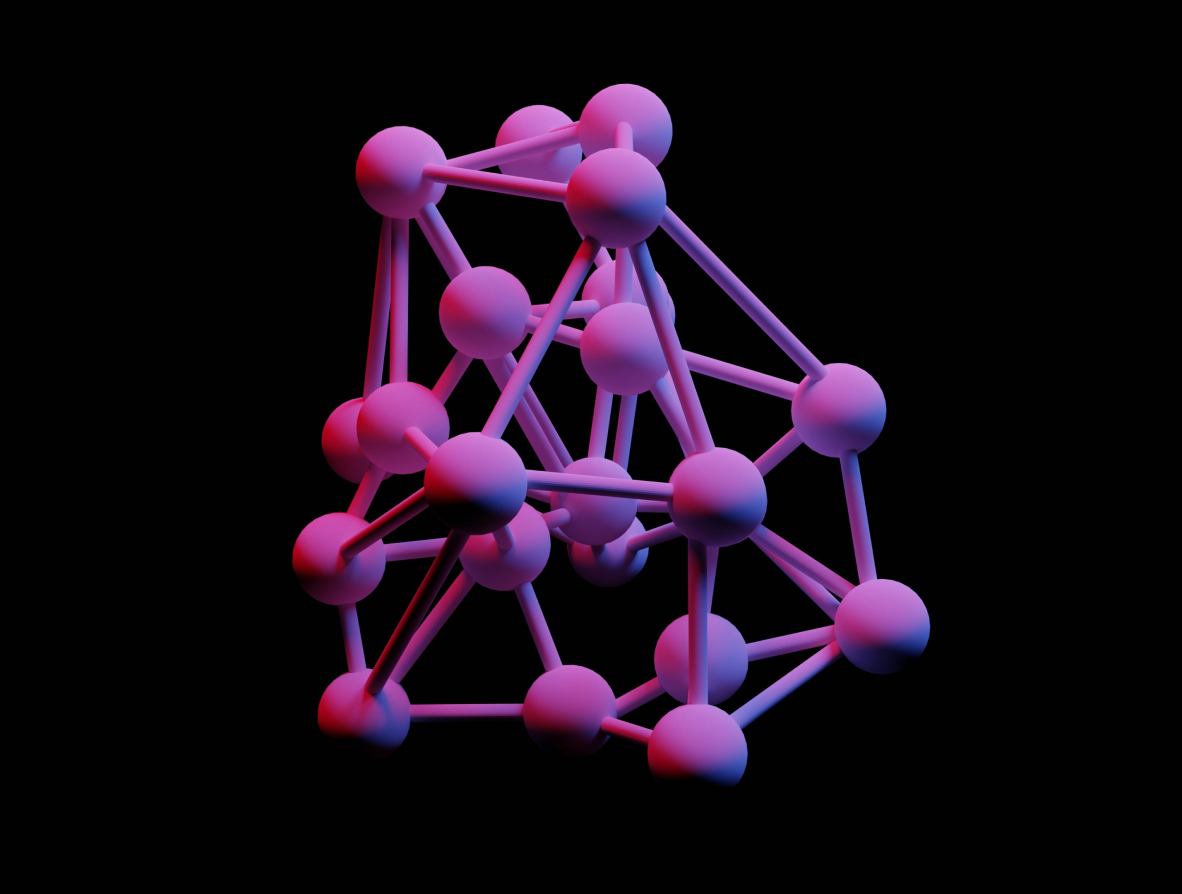
Articles
Exploring the potential of LLMs in robotics: an interview with Louis Dumas
Robotics has always been at the forefront of technological advancement, but translating human ideas into robotic actions remains one of its greatest challenges. In an interview with Louis Dumas, co-founder and CTO of inbolt, he shared his insights into the transformative potential and current limitations of Large Language Models (LLMs) in the robotics field.