What is a Digital Twin?
A digital twin is a virtual representation of a real-world entity, or a system that connects the physical asset (whichever item is in the real world) with capturable data (in the digital world). It is created using CAD (computer-aided design) data.
There is a new buzzword in the industry, and it’s “digital twin”.
A digital twin is a virtual representation of a real-world entity, or a system that connects the physical asset (whichever item is in the real world) with capturable data (in the digital world). It is created using CAD (computer-aided design) data.
Digital Twin with CAD
On a smaller scale, a digital twin can be a CAD model of a single part or component. The digital twin accurately reflects the part's dimensions, properties, and behavior, mirroring its real-world counterpart as closely as possible.
On a macro level, digital twins can scale up to create an entire 3D virtual model of a complex system, like manufacturing plants. In this case, the model will encompass every machine, conveyor, and workflow within the plant, all interconnected and dynamically updating in real-time. The 3D virtual plant will serve as a comprehensive digital platform for predicting system behavior, testing new strategies, and performing preemptive maintenance, hence facilitating operational efficiency and cost-effectiveness.
On a smaller level, digital twins can also be the CAD model of parts that will be manufactured.
On a more granular scale, digital twins serve as the advanced CAD models of components earmarked for production. This technology not only aids manufacturers in meticulously strategizing their manufacturing processes but also acts as a simulation tool. It enables the testing of actions and stresses on various parts to analyze how different materials and assemblies respond under specific conditions, for instance, within combustion engines. This level of foresight and predictability significantly enhances the efficiency and effectiveness of the production process.
At its core, a digital twin is a proxy of the real world, accessible online through IoT, which allows companies to test out scenarios in the cloud before testing it out in the real world. By creating a virtual representation of a system, it's possible to predict outcomes, reduce uncertainties, and make more informed decisions.
Benefits
One of the major benefits of a digital twin is the ability to analyse and evaluate potential risks before they happen. These digital counterparts are not static; they're designed to mimic their real-world counterparts in real-time, updating themselves with data from various IoT sensors and other sources. This allows industries to adopt a proactive approach rather than a reactive one.
In the manufacturing industry, a digital twin can simulate how new production line changes might impact overall efficiency, safety, or cost by testing the situation digitally. Not only does it remove any risk of damaging the actual equipment, but it can also increase the likelihood of success by identifying bottlenecks, or testing out various configurations to get to the most advantageous one.
This is particularly useful in industrial robotics. Companies such as Siemens and Nvidia sensed the need among their customers and developed products powering the use of digital twins among industrials.
A Case of Tecnomatix
When it comes to offline programming and simulation, digital twins have been growing in popularity. A compelling illustration of this lies with Process Simulate on Teamcenter, an integral part of Siemens Tecnomatix.
This tool allows industrial entities to virtually design, streamline, and verify production systems by crafting a digital footprint of the manufacturing environment, which facilitates virtual commissioning and ensures the processes perform as planned.

Nvidia's Isaac SIM
Embracing the power of 3D digital twins, Nvidia's Isaac SIM – a virtual robotics laboratory and high-fidelity physics simulator – has taken the concept to a whole new level. Isaac SIM provides a platform for training digital twins, simulating a wide range of physical environments, scenarios, and conditions.
Nvidia's Isaac SIM uses state-of-the-art technology to replicate real-world physics, allowing developers to train and test their robotic systems in safe, virtual environments before deploying them in the real world.
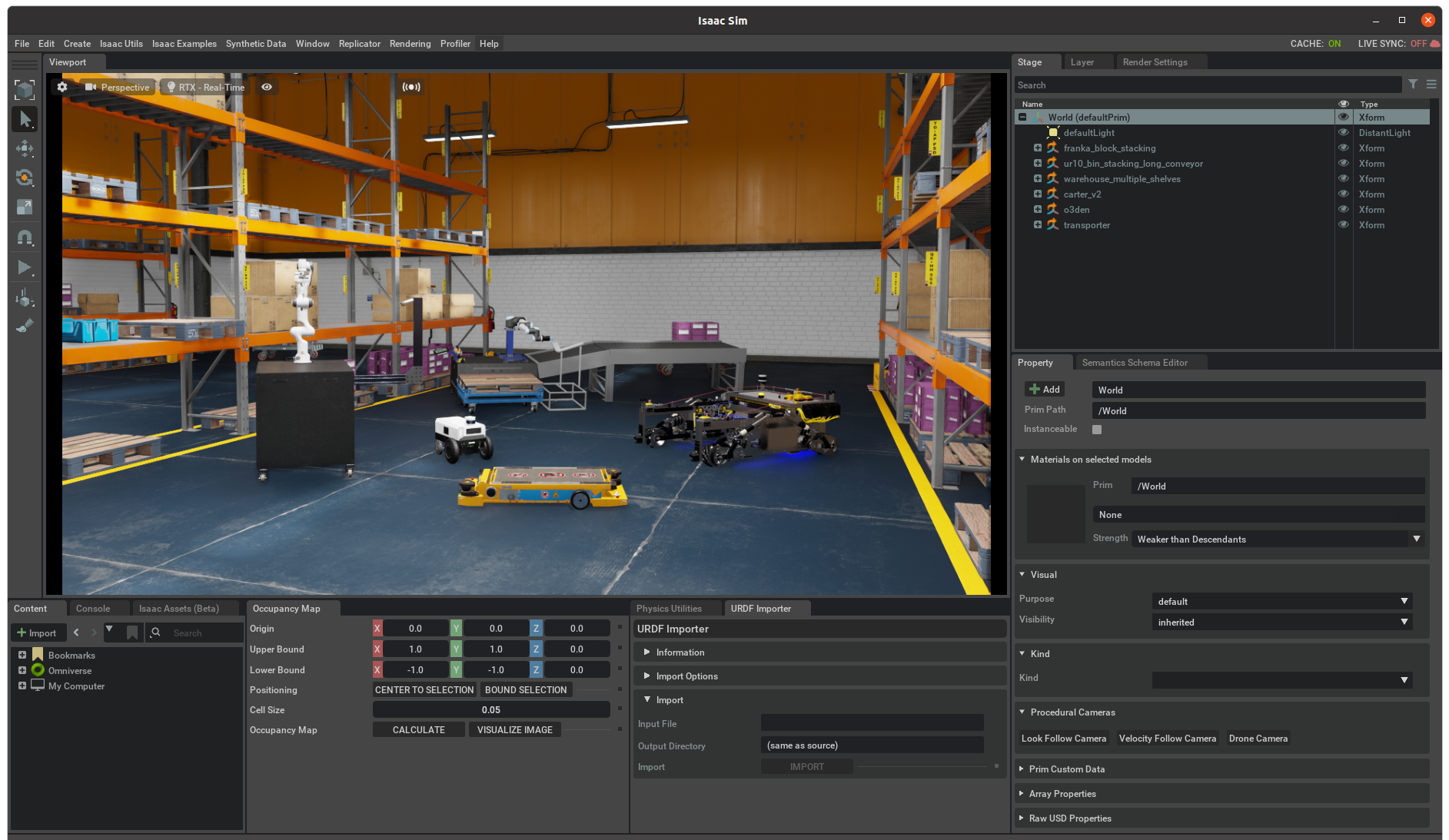
Addressing the Mismatch Between Reality and Digital Twins
The argument "reality never matches the digital twin" carries some truth: no model can perfectly mirror every aspect of reality. While the digital twin offers an incredibly precise representation of a physical part, it can't fully account for the dispersion, or variation, in the piece itself. A physical part is influenced by many factors - from the quality of materials, the precision of machinery, environmental conditions, to human errors - that are not always replicated accurately in a digital environment.
However, the value of digital twins is not diminished by this fact. Digital twins still expedite processes by a landslide compared to the existing systems that exist today.
And with the progress of AI, algorithms that train on datasets derived from these digital twins are progressively improving their capacity to adapt to real-world variations. They can recognize and respond to unexpected events like collisions or non-quality elements.
The gap between digital twins and reality is constantly narrowing, thanks to AI's evolution. It's a matter of time before AI enables robots to adapt seamlessly to discrepancies between the digital twin and the actual environment.
Conclusion
Despite some level of mismatch between the virtual and physical worlds, the value proposition of digital twins - saving time, enabling simulations, centralizing information, and improving training of AI algorithms - remains significant and continues to expand with technological advancements. The gap between digital twins and its real-world equivalent is bound to narrow, leading to more precise and realistic digital models as time goes on.
Robin Dechant, who we interviewed a few weeks ago, confirmed that digital twins were a trend expected to expand in the coming years.
Read his interview here.
Reach out to us to discuss your automation needs.
Last news & events about inbolt
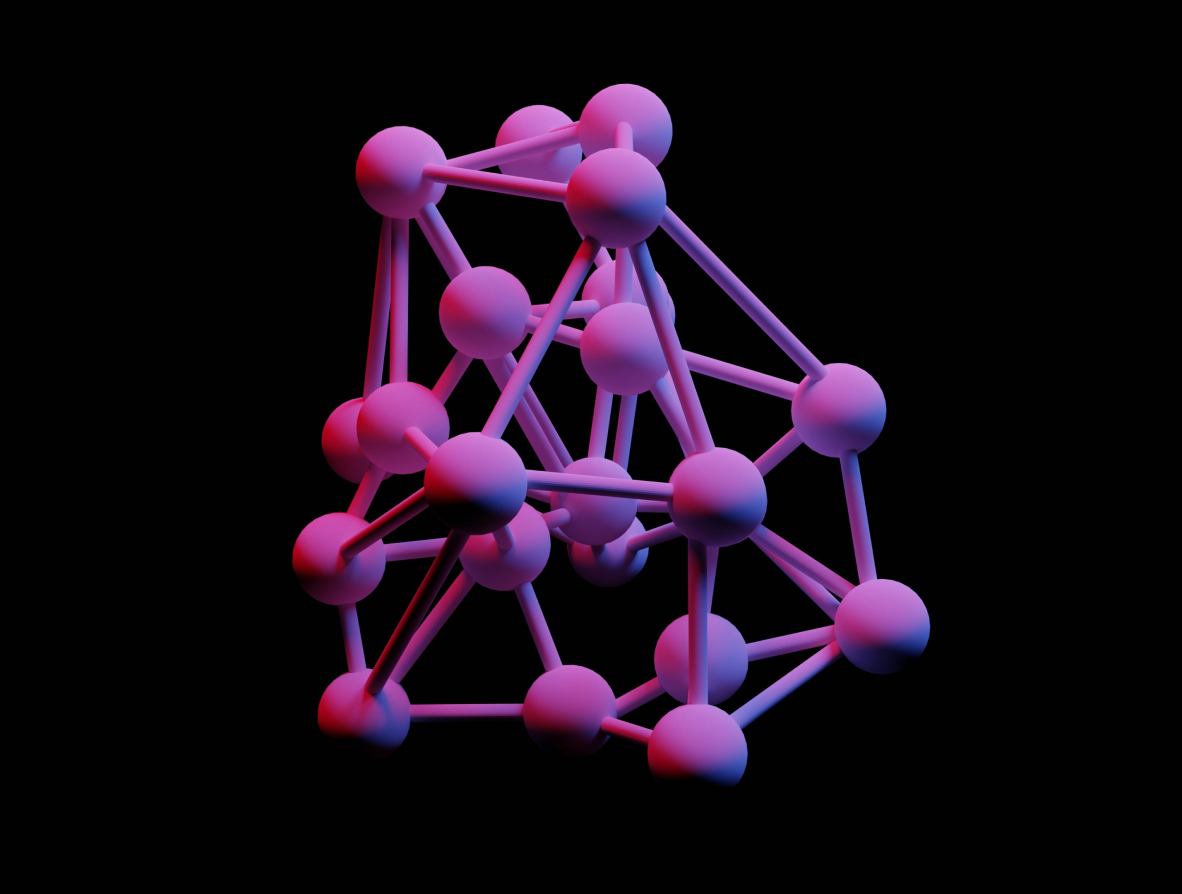
Articles
Exploring the potential of LLMs in robotics: an interview with Louis Dumas
Robotics has always been at the forefront of technological advancement, but translating human ideas into robotic actions remains one of its greatest challenges. In an interview with Louis Dumas, co-founder and CTO of inbolt, he shared his insights into the transformative potential and current limitations of Large Language Models (LLMs) in the robotics field.