Robotic Programming
Diving into the world of robot programming, from choosing the right language to innovative AI techniques.
An Introduction to Robot Programming
Robot programming, at its core, is the art of converting an idea into a series of automated actions for a robot.
From the Roomba to the industrial robot built to perform intricate tasks (sanding, welding, etc), the range and complexity of the tasks that can be handled through robotic programming are incredibly diverse.
And with the arrival of cobots, the range has just kept on increasing, allowing SMBs to dive into robotics with a lower budget, and expanding the various use cases that robots can have to help both large and medium sizes industries with their automation needs.
Where to Begin
The field of robotic programming is a profession in itself, and breaking into it entails making several essential decisions:
- Programming Language Selection: Your choice of programming language would depend on the robot type and its intended tasks. The most used languages tend to be Python (simple and easy to use), C++ (efficient and speedy, mostly used for real-time and resource-constrained applications), and Java (platform independent and extremely modular).
- Choosing the Right Programming Environment: Selecting an integrated development environment (IDE) that meets your requirements is, arguably, the most important step. The Robot Operating System (ROS) is usually a common choice, as it’s equipped with tools and libraries designed to help with the creation of robust and durable robot behavior.
- Picking a Programming Method: Options include offline programming (in a simulated environment), online programming (while the robot is operational), or lead-through programming (where you manually guide the robot through the desired movements).
- Required Programming Plugins: Some tasks may necessitate the use of specific software plugins. Within the robotic programming realm, many solutions exist that can help analyze and understand external data from sensors. GuideNOW, an inbolt patented software, adapts the robot's trajectory in real-time thanks to 3D vision.
Demystifying the Robotic Programming Process
The process of robotic programming involves a sequential progression through multiple stages:
- Task Definition, in order to outlines the robot's expected tasks, which can range from simple tasks like a Roomba's cleaning routine, to intricate industrial processes such as sanding or welding for automotive industry, for instance.
- Trajectory Planning, to determine the robot's path to complete its tasks. It will cover starting and ending points, intermediate points, and any obstacles to be avoided. Most of the time this is performed in a virtual environment.
- Program Generation, where the tasks are converted into a robot-understandable program that is then loaded onto the robot's controller once the trajectory has been validated.
- Program Optimization, to refine the program: adjusting the robot's speed, path, etc, to enhance the task performance with regard to the real-world.
In robot programming, the one essential aspect to keep in mind is collision avoidance, which refers to the capability of a robot to detect and avoid obstacles or collisions in its environment. It is crucial for ensuring the safety of the robot, preventing damage to itself and its surroundings, and avoiding potential accidents. It will do so using sensors (lidar, proximity, cameras), through environment mapping (to understand the locations and shapes of obstacles), and via path planning. Once the robot has sensed the environment and mapped the obstacles, it can plan a collision-free path.
Both these aspects are vital for safe and efficient robot operation.
Read our article on the Standardization in robot programming, the challenges and opportunities here.
Advanced Concepts in Robot Programming
In the evolving field of robotics, one focus area that has become especially important is robot perception. Robot Perception is the capacity of a robot to comprehend its surroundings or the workpiece itself, enabling them to function more effectively and autonomously. This includes methods such as Simultaneous Localization and Mapping (SLAM), that are crucial for mobile robots, as well as vision-based robot guidance solutions utilized for industrial robots. These solutions allow robots to create comprehensive representations of their environment, facilitating tasks such as navigation, object manipulation, and interaction. These methods leverage a broad spectrum of sensors, ranging from 2D and 3D visual sensors to sophisticated force sensors.
There is also a burgeoning trend towards harnessing artificial intelligence for easier robot programming. Drawing from the insights shared in a recent Google AI blog article titled "Robots that Write Their Own Code", AI integration could revolutionize robot programming by enabling robots to self-code based on the task at hand. Although it's still in the early stages of development, this trend promises possibilities for the future.
Robotic programming is an expansive profession. With the rapid advancements in technology, robots are becoming more sophisticated, leading to more complex programming roles. The scope of robot programming keeps extending, from autonomous vehicles to surgical robots, and the demand for skilled robot programmers is on the rise. This trend is expected to continue as more and more robots flood various industries.
Last news & events about inbolt
.png)
Articles
Inbolt and FANUC Pioneer Robots that Think and Act on the Fly at Moving Assembly Line Speeds
Inbolt and FANUC are launching a manufacturing breakthrough enabling FANUC robots to tackle one of the most complex automation challenges: performing production tasks on continuously moving parts at line speeds. With Inbolt’s AI-powered 3D vision, manufacturers can now automate screw insertion, bolt rundown, glue application and other high-precision tasks on parts moving down the line without costly infrastructure investments or cycle time compromises.
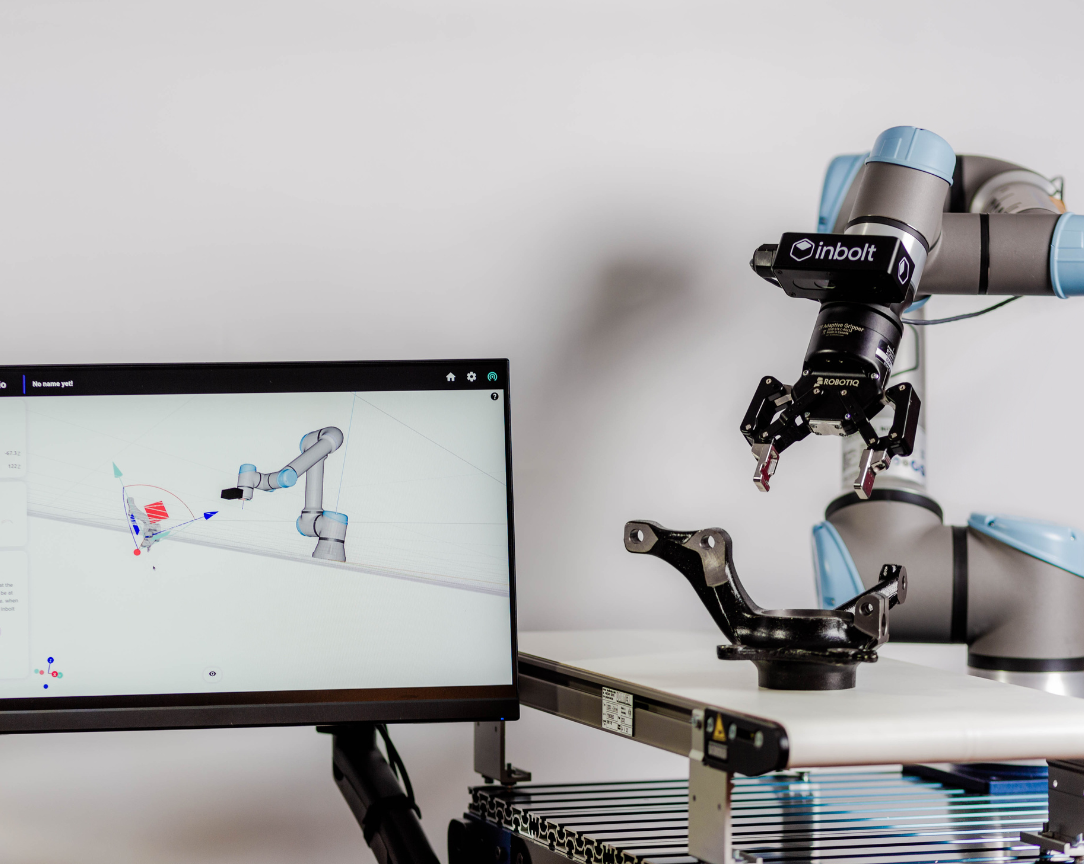
Articles
Sim2Real Gap: Why Machine Learning Hasn’t Solved Robotics Yet
The most successful areas of application for deep learning so far have been Computer Vision (CV), where it all started, and more recently, Natural Language Processing (NLP). While research in Robotics is more active than ever, the translation from research to real-world applications is still a promise, not a reality. But why?