Industry 5.0
What is Industry 4.0, and what will Industry 5.0 look like?
Industry 4.0 was first coined in Germany in 2011. Just over 4 years later, we were already hearing whispers of Industry 5.0. Although it was first breathed in 2015, the interest has only grown since.
Thus far, there has not been any industrial revolution that has happened so close together, though we can definitely observe a pattern of each revolution coming closer and closer to the previous one.
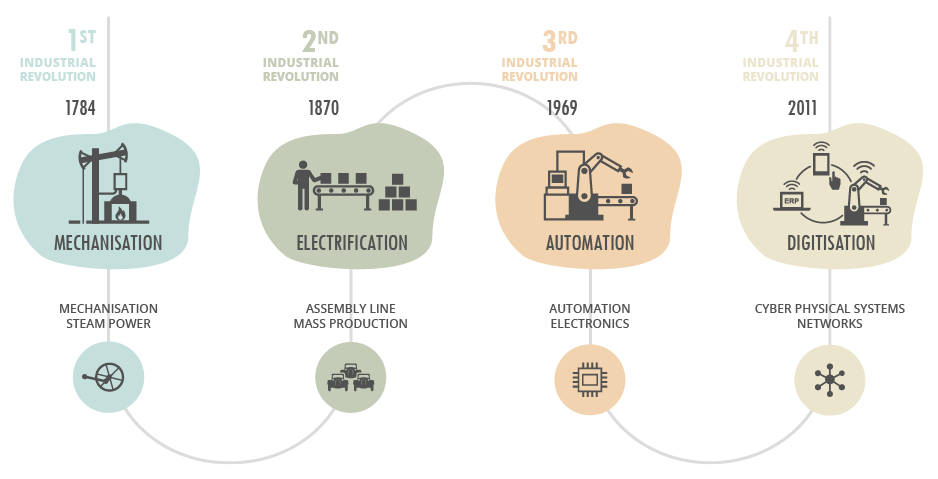
Today, I want to compare and discuss 4.0 and 5.0.
The first two industrial revolutions focused mainly on scalable efficiency, while the third and fourth focused more on scalable adaptability. We spent three industrial revolutions empowering corporations, and are now looking to re-empower people and save the planet.
And at the heart of it all, differences between 4.0 and 5.0 are subtle (this is also why some experts do not consider 5.0 to be real, as 4.0 has shortcomings that 5.0 is solving. And, since they’re so close together, some people insists on combining them both as one).
Robots aren’t going anywhere, obviously. Pandora’s box is well and truly open. The best we can (and should) do, is ensuring that our creations empower humans, not replace them. The use of cobots in small and medium-sized businesses (SMBs) will become more prevalent as the technology becomes more accessible and cost-effective, allowing them to stay competitive in the global market.
This is the heart of 5.0.
The incredible arrival of cobots in robotics will play a crucial part in this system, handling the iterative tasks and leaving humans to focus on perception-driven decisions. These cobots will be designed to assist and improve the efficiency of human workers, rather than replacing them.
While 4.0’s main focus was mass production at all costs to increase global competitiveness (think work 24/7), this system often resulted in a lack of customization and flexibility in the manufacturing process.
5.0 will see an ever-increasing number of cobots both in large and SMBs to meet personalization at scale in manufacturing by leveraging artificial intelligence (AI) and the Internet of Things (IoT). Machine learning algorithms will be trained to recognize patterns and make predictions based on data, allowing companies to adjust the production schedule, improving efficiency and helping to reduce waste. IoT will provide real-time information (like tracking the usage of products and gather data on customer preferences) to improve the design and personalization of products.
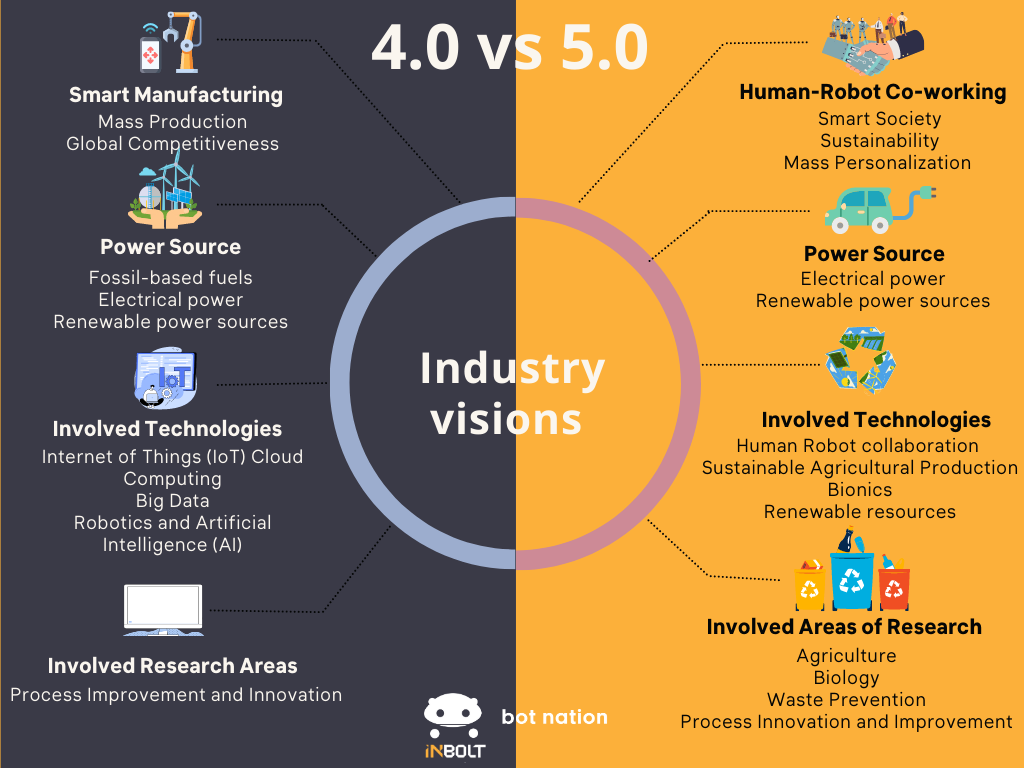
While Germany lead the fourth industrial revolution, the consensus is that the US might be leading the new, “Smart Factory” era. The US is home to many of the world's leading technology companies (Apple, Microsoft, Google), which are driving innovation in AI, IoT, and advanced analytics. The US government has also been actively supporting Industry 5.0 through initiatives such as the National Strategic Plan for Advanced Manufacturing (which aims to promote the development and adoption of advanced manufacturing technologies). Not only that, but the US has a strong startup ecosystem working on new technologies such as Augmented Reality, Blockchain and Edge computing, which could be the key enablers for Industry 5.0.
So, what can we expect in 2025?
- Turnkey solutions, with companies specializing in creating new applications and products using existing technologies. One example of this is Enabled Robotics, working to integrate cobots with autonomous mobile robots (AMRs). This combination of cutting-edge technologies allows for increased automation and collaboration in the manufacturing process, enabling greater personalization at scale.
- As more industries adopt automation to solve issues with supply chains and labor shortages, the demand for intelligent robots is expected to grow. One major trend includes the development of robots that can operate in dynamic environments.
- The cobot industry’s growth to a whooping USD 2.2 billion by 2026, with more and more companies turning to cobots.
- Increased use of simulation and virtual reality (VR) in manufacturing to test and optimize the manufacturing process before it is implemented in the real world, reducing the risk of errors and downtime.
- More widespread use of predictive maintenance. By using data from sensors and other sources to predict when equipment is likely to fail, manufacturers can schedule maintenance before a problem occurs, reducing downtime and costs.
- Greater adoption of advanced analytics and artificial intelligence (AI) in manufacturing to,analyze data and make predictions about the manufacturing process.
- Increased connectivity with the IoT, which will help to connect machines, devices, and systems, providing real-time data and insights into the manufacturing process.
- Greater use of blockchain technology for supply chain traceability, which will enable manufacturers to quickly and easily track the origin of raw materials and components, as well as the movement of finished goods through the supply chain.
- Have anything to add the to list? Let us know!
Last news & events about inbolt
.png)
Articles
Inbolt and FANUC Pioneer Robots that Think and Act on the Fly at Moving Assembly Line Speeds
Inbolt and FANUC are launching a manufacturing breakthrough enabling FANUC robots to tackle one of the most complex automation challenges: performing production tasks on continuously moving parts at line speeds. With Inbolt’s AI-powered 3D vision, manufacturers can now automate screw insertion, bolt rundown, glue application and other high-precision tasks on parts moving down the line without costly infrastructure investments or cycle time compromises.
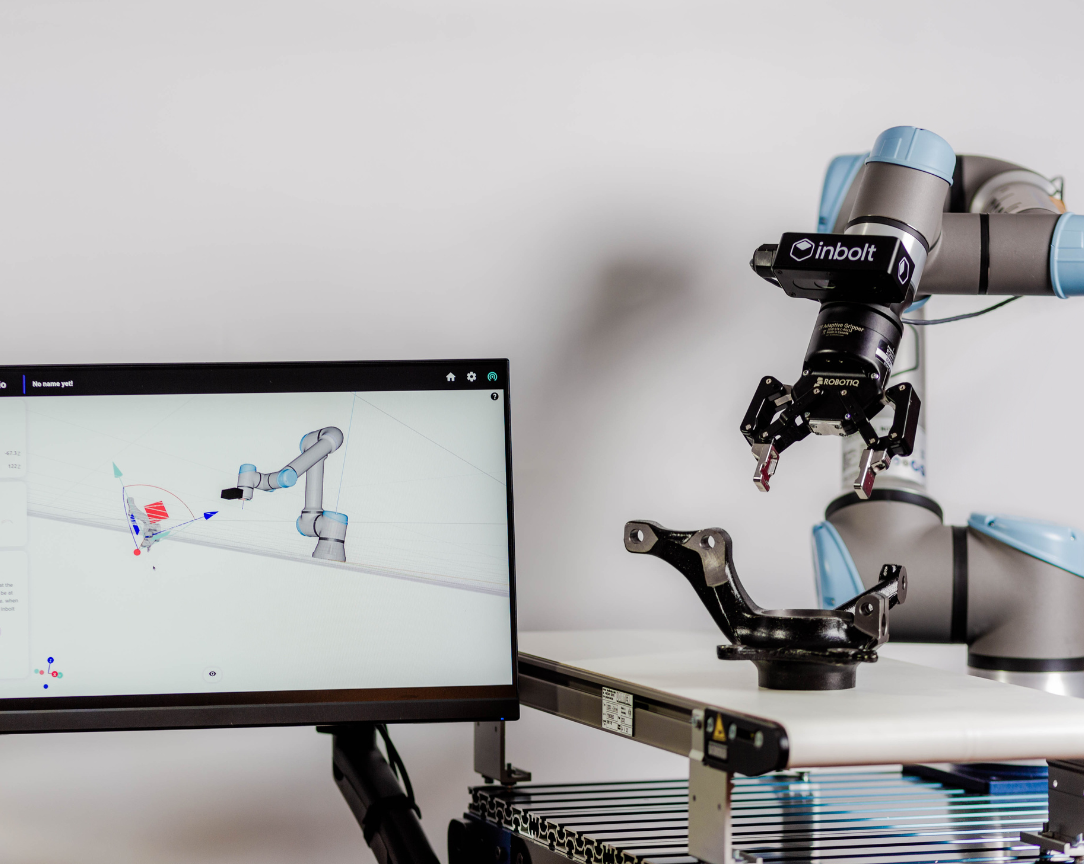
Articles
Sim2Real Gap: Why Machine Learning Hasn’t Solved Robotics Yet
The most successful areas of application for deep learning so far have been Computer Vision (CV), where it all started, and more recently, Natural Language Processing (NLP). While research in Robotics is more active than ever, the translation from research to real-world applications is still a promise, not a reality. But why?