Cobots in Manufacturing
While cobots are currently only taking a small part of the robotic market at present, predictions are indicating that by 2025, cobots will account for 34% of all robots sold on the market. In 2021, the global collaborative robot market was valued at US $894.60 million, with an expected rise to US$3.21 billion in 2026, and USD 7 billion by 2030. Judging by the rising number of companies throwing their hats in the cobot market, it’s evident that everyone wants a piece of the cake.
Cobots in Manufacturing
With their first introduction in 2008, cobots have experienced a steady growth, notably in the manufacturing sector.
While cobots are currently only taking a small part of the robotic market at present, predictions are indicating that by 2025, cobots will account for 34% of all robots sold on the market. In 2021, the global collaborative robot market was valued at US $894.60 million, with an expected rise to US$3.21 billion in 2026, and USD 7 billion by 2030. Judging by the rising number of companies throwing their hats in the cobot market, it’s evident that everyone wants a piece of the cake.
One of the fundamental differences between traditional industrial robots and cobots is their ability to work alongside human workers. Cobots are power-and-force-limited (PFL), which means they are safe to use around humans and can share the same workspace without the need for cages, which in turn can enhance productivity by up to 24.3%.
Why Cobots?
- Partial Automation: Cobots can handle repetitive parts of tasks, allowing human workers to focus on more skill-intensive aspects.
- Space-Efficient: Without the requirement for cages, cobots save significant floor space.
- Rapid Deployment: Cobots are easy to program and plan for, allowing for a rapid implementation.
- Cost-Effective: Cobots are, generally speaking, a more economical choice in the long run. They demand less infrastructure, lower training expenses, are easier to maintain, and easier to scale or re-program when/if needed.
Essentially, their versatility makes them incredibly practical in the industry, especially considering the uphill trend of high mix low volume. And while their arrival brought about some concerns regarding the status quo maintained in the manufacturing industry, it’s becoming obvious that cobots and traditional robots are expected to each work on different tasks, each complementing the other by solving different issues within the manufacturing floor.
Automation is not just about robots. There is a delicate and complex ecosystem surrounding the entire process that involves more than just the robot and the people manufacturing them. Read our article about Cobot Ecosystems.
Differences and Similarities
Since their popularity increase, large companies and SMEs alike started introducing their versions of the cobots on the market and have come up with various types of cobots equipped for specific tasks that other cobots on the market aren’t capable of doing (think mini-cobots), while settled and renowed companies have created their own version of cobots, compatible with all of their other products.
The truth is that the market isn’t oversaturated yet, and while it’s been a little under ten years, there aren’t any cobot brand aside from Universal Robots that have become a household name yet.
There are multiple factors contributing to this trend. Firstly, Universal Robots stands out as the pioneering force, introducing their initial collaborative robot (cobot) back in 2008. Since then, they've expanded their product line to encompass seven different sizes and payload capacities.
Secondly, their creation of an extensive ecosystem revolving around the brand is a game-changer. This ecosystem nurtures seamless integrations with third-party solution providers, including grippers and vision systems. To join the coveted UR+ ecosystem, the primary requirement is to offer plug-and-play compatibility for end-users, streamlining the deployment of comprehensive solutions.
The Expansion
Universal Robots released their first cobot in 2008, and steadily kept releasing new versions every few years. In contrast, barely any cobots from other brands were released until 2013 with KUKA, followed in 2015 by ABB, FANUC, Yaskawa, Kassow, Precise Automation. In 2016, Staubli followed along with Techman robots and AUBO robotics. 2018 saw the arrival on the cobot market of Kawasaki, Mitsubishi Electric and Neura robotics.
This still leaves an almost seven year gap between 2008 and the first UR robot and 2013 with KUKA’s first cobot release, leaving ample time for UR to position themselves as leaders in the market.
But despite the competition, the market to penetrate remains large and, most importantly, will continue to grow. Labor shortages, the increase in labor costs, the reshoring trend, and the growing interest for flexible automation is creating an evident need for these types of collaborative robots. And not only is the market not saturated yet, but the technology keeps getting better, leaving room for more and more innovation to be fitted in, on, or around these cobots.
Some brands are offering a unique version with their own unique selling points:
- Techman Robots was the first to introduce an integrated vision system.
- AUBO Robotics' computer system is adaptable to a number of coding languages.
- Robco provides modular cobots.
- Several brands, like FANUC and OMRON, emphasize compatibility and integration with their existing equipment or systems, encouraging their clients to remain loyal to their brand.
Most brands have at least a few versions of their most popular cobots, but with different payloads, from 0.5kg to 35kg, allowing cobots to cater to a variety of tasks in the industry, and almost all brands emphasize features like precision, user-friendliness, and efficiency, which are critical market demands. Cobots, by design, are required to be user-friendly.
Brands like OMRON and Doosan Robotics have only recently entered the market (2022 and 2020 respectively) but offer a considerable number of cobot variants. This shows that even as a relatively newer entrant, companies can quickly establish a strong foothold if they cater to the existing market demands.
The Future of Cobots
Cobots may currently represent a smaller cut than industrial robots, but it appears evident that the manufacturing industry has recognized their usefulness. The wide array of capabilities reinforces the notion that cobots are more than just a fleeting trend. They are reshaping the manufacturing landscape, offering businesses a competitive edge in an increasingly automated world. As the manufacturing world gravitates towards more flexible and adaptive solutions, cobots will surely be a strong part of this transformation.
Here at inbolt, we hold a firm conviction that with the emergence of new robot and cobot brands, the demand for vision-based robot guidance systems will continue to surge. As manufacturers tirelessly pursue enhanced flexibility and cost-effective automation, this drive proves to be a boon for both the cobot and vision guidance system markets. We eagerly anticipate the forthcoming years, poised to witness the remarkable growth of the industrial robotics sector.
The future is indeed promising!
And because we want to share our knowledge, here is a table of some recent cobot launches. Let us know if we forgot some!
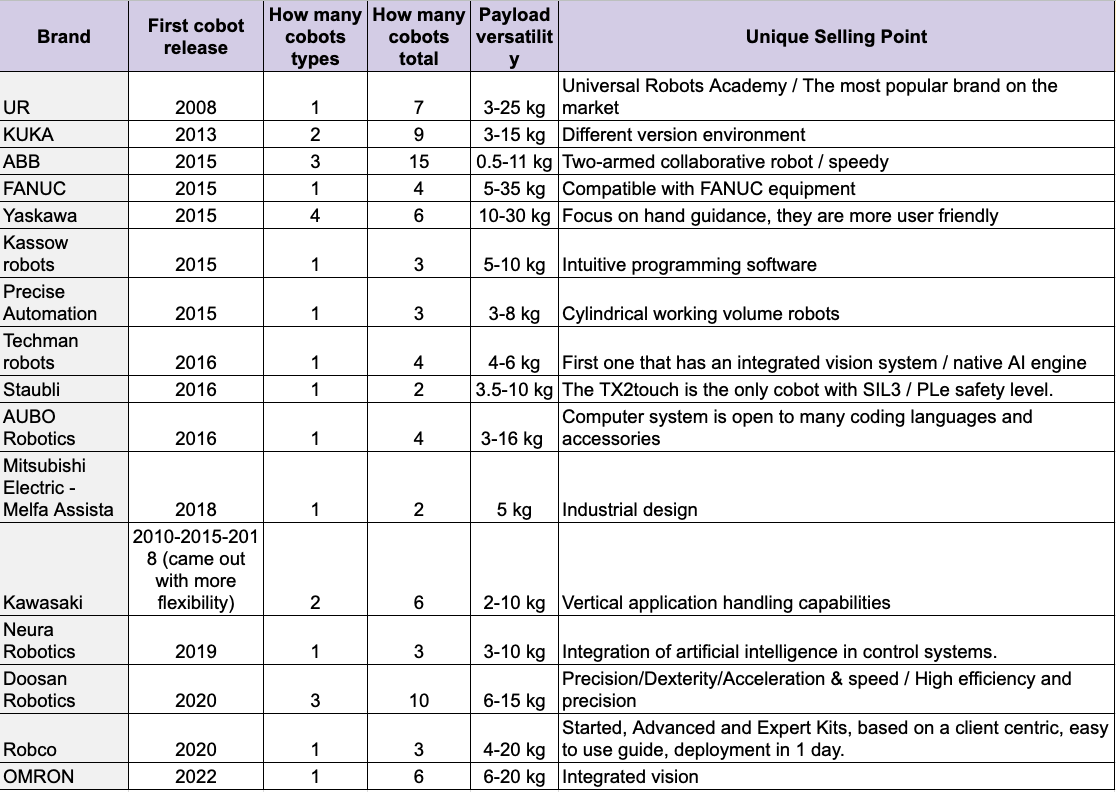
Reach out to us to discuss your automation needs.
Last news & events about inbolt
.png)
Articles
Inbolt and FANUC Pioneer Robots that Think and Act on the Fly at Moving Assembly Line Speeds
Inbolt and FANUC are launching a manufacturing breakthrough enabling FANUC robots to tackle one of the most complex automation challenges: performing production tasks on continuously moving parts at line speeds. With Inbolt’s AI-powered 3D vision, manufacturers can now automate screw insertion, bolt rundown, glue application and other high-precision tasks on parts moving down the line without costly infrastructure investments or cycle time compromises.
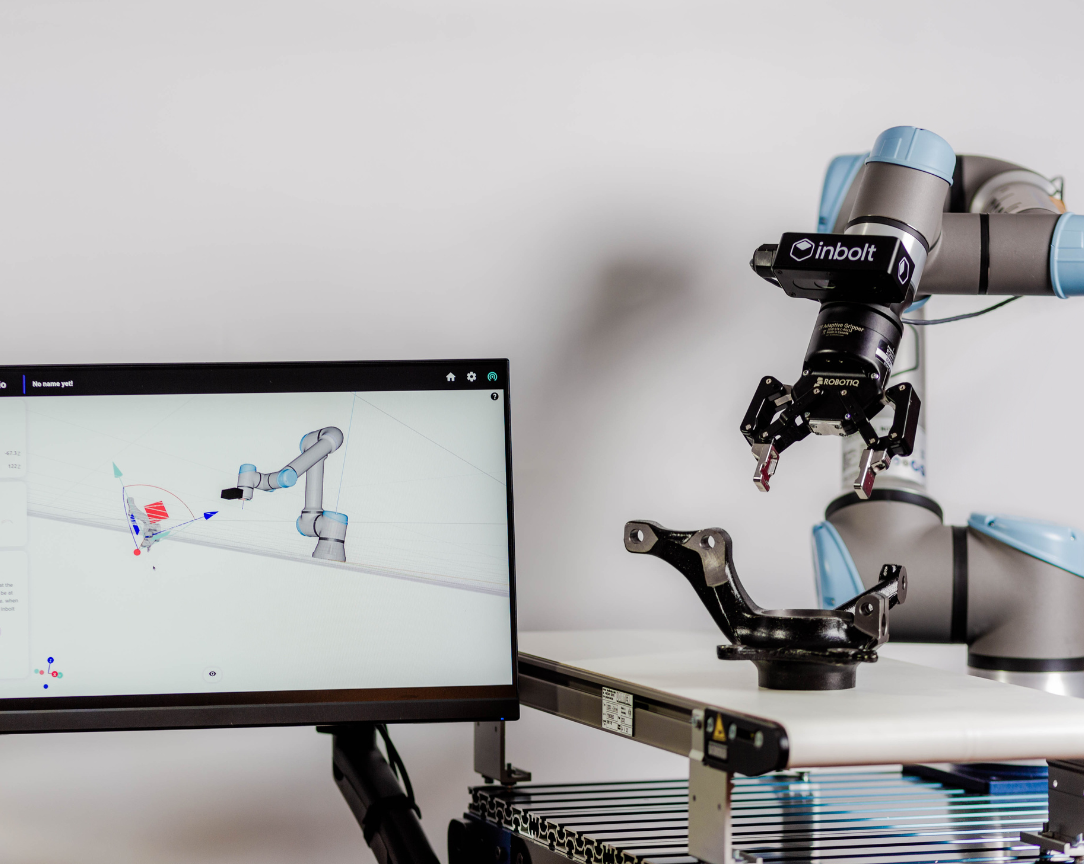
Articles
Sim2Real Gap: Why Machine Learning Hasn’t Solved Robotics Yet
The most successful areas of application for deep learning so far have been Computer Vision (CV), where it all started, and more recently, Natural Language Processing (NLP). While research in Robotics is more active than ever, the translation from research to real-world applications is still a promise, not a reality. But why?