A Comprehensive Guide to Calculating the ROI of a Robotic Cell
The integration of robotic cells has proven to be a game-changer for businesses. However, it's important to assess the return on investment (ROI) before implementing a robotic cell. In this article, we explore the ROI of automating a manual mastic application workstation on a moving line and the benefits of using inbolt's GuideNOW. Learn how to take the first step towards optimizing your manufacturing process.
The integration of robotic cells in manufacturing processes has proven to be a game-changer for businesses. It has helped businesses achieve high efficiency, accuracy, and productivity while reducing labor costs and non-quality costs. That being said, the initial cost of automation is usually a cause for concern, and businesses need to assess the return on investment (ROI) before implementing a robotic cell.
More recently, there has been more and more pressure put on the reduction of manufacturing costs, forcing industrial companies to aim for a faster ROI. In some industries, the target for ROI has been reduced from three years to less than one year.
This puts a strain on the current state of automation and is further encouraging companies to turn to automation.
Calculating ROI can be a daunting task, especially for a first time, but it is essential, as it will allow the company to not only know if the investment in automation is worth the cost but it will also allow them to work through various existing automation systems to determine the best for their specific needs.
How to Compute a Return on Investment
In the cobweb that is computing automation ROI, the following benefits and costs should be taken into account:
Total Benefits of Automation
The benefits of automation, regardless of the system put in place, include:
- Increased accuracy and precision
- Consistent cycle times
- Reduced variability in the manufacturing process
- Improved safety for workers
- Reduced labor costs
- Improved quality of the finished product
Total Cost of Automation
The total cost of automation includes both non-recurring and recurring costs:
- Non-Recurring Costs: These are one-time costs associated with the implementation of the robotic cell:
- Hardware equipment: robot, cell, effector, jig, additional equipment, table, cables, PLC, encoders
- Integration services: training and integration days
- Recurring Costs: These are ongoing costs associated with maintaining and operating the robotic cell. Such costs especially arise when launching a new reference in production:
- Trajectory re-programming
- Vision system re-programming
- New jigs
- Maintenance
Impact on Productivity
When considering the impact on the productivity of automating a manual workstation. Indeed the cycle time of the workstation should remain the same or, at least, the flow of the line should be equilibrated.
This is particularly the case for automating manual assembly workstations on moving lines. When changing such a station into a fixed robotic station, one must take into account the time it takes for the part to move from the moving line to the fixed station.
Do you want to create your own ROI calculator?
Contact us, and we’ll send you the template for your own ROI calculation.
Example – Automating a manual mastic application workstation on a moving line
Context
For the purpose of this ROI calculation, we will take the use case of the automation of mastic application on a moving line, aimed at improving the efficiency of a car manufacturing assembly line.
All the nitty gritty calculations, as well as our hypotheses, will be made available on request by filling out the form.
The customer, a car manufacturer, currently has a legacy assembly line with manual workstations on a moving line.
One of the mastic application workstations needs to be automated due to the high volume and low diversity of parts manufactured.
The project involves computing the different ROIs the customer can achieve with three different ways to automate the workstation:
- Automating into a fixed workstation (stop-and-go line)
- Automating the workstation on the moving line with traditional equipment
- Using GuideNOW with Inbolt to automate the moving line
The circumstances surrounding the project include a moving workpiece, manual legacy system, low mix, and very high volume of parts manufactured in France.
For this scenario and for simplification, we computed solely the initial total cost of automation, i.e., the non-recurring costs of the different automation options.
The expected benefits for the customer rely mostly on the reduction of labor costs.
Automating into a fixed station
- The total cost of automation: approx. 70k€
- Productivity : -14%
Cost of automation
On top of all the required components to automate the cell (robot, PLC, end-effector, etc.), there is an additional need for handling equipment in this scenario to transport the workpiece from the moving line to the fixed workstation. This proves expensive, takes up space, and lacks flexibility, thus driving high investment.
Impact on productivity
A fixed workstation involves a travel time of the workpiece between two stations. During this time, as no operation is performed on the car, such time is lost.
Usually moving from moving workstation to fixed requires a complete change in the entire process, leading to productivity loss and a necessary rebalancing of the line.
We anticipate a 14% decrease in productivity compared to the manual station. This means that the total number of cars going through the station per year will decrease due to the implementation, at least for a time.
Automating the workstation on the moving line with traditional equipment
- The total cost of automation: approx. 110k€
- Productivity: same as for the moving line, should the step cycle not change
Cost of automation
Automating a moving line with traditional equipment requires a heavy infrastructure which includes: encoders, sensors, etc. In such cases, a mobile jig that allows the robot to attach itself to the moving tooling carrying the workpiece is required to make sure the robot performs the process properly on the part. Such equipment is very expensive and constraining, resulting in high integration costs.
The productivity of the cell will remain the same as the manual station as there is no change in the process other than the addition of the robot.
Automating the Moving Line with Inbolt
- The total cost of automation: approx. 55k€
- Productivity: same as for the moving line, should the step cycle not change
Automating a moving line is the most expensive endeavor, but switching to Stop-and-Go will generate a loss of productivity in the cell and a necessary rebalancing of the line.
One of the most advantageous options for automating a moving line is pairing it with a real-time industrial robot guidance system like Inbolt.
Inbolt’s solution, GuideNOW, offers flexibility and is workpiece-centric, making it easy to set up thanks to a CAD model of the workpiece. This means there’s no need to constrain the environment (jigs) or use markers, which is especially useful for customers with high productivity.
Additionally, GuideNOW is hardware-independent and can work on any 3D vision camera, allowing for adaptation to different use cases through parameter optimisation.
Reach out to us for access to the template, and take the first step towards optimising your manufacturing process.
Last news & events about inbolt
.png)
Articles
Inbolt and FANUC Pioneer Robots that Think and Act on the Fly at Moving Assembly Line Speeds
Inbolt and FANUC are launching a manufacturing breakthrough enabling FANUC robots to tackle one of the most complex automation challenges: performing production tasks on continuously moving parts at line speeds. With Inbolt’s AI-powered 3D vision, manufacturers can now automate screw insertion, bolt rundown, glue application and other high-precision tasks on parts moving down the line without costly infrastructure investments or cycle time compromises.
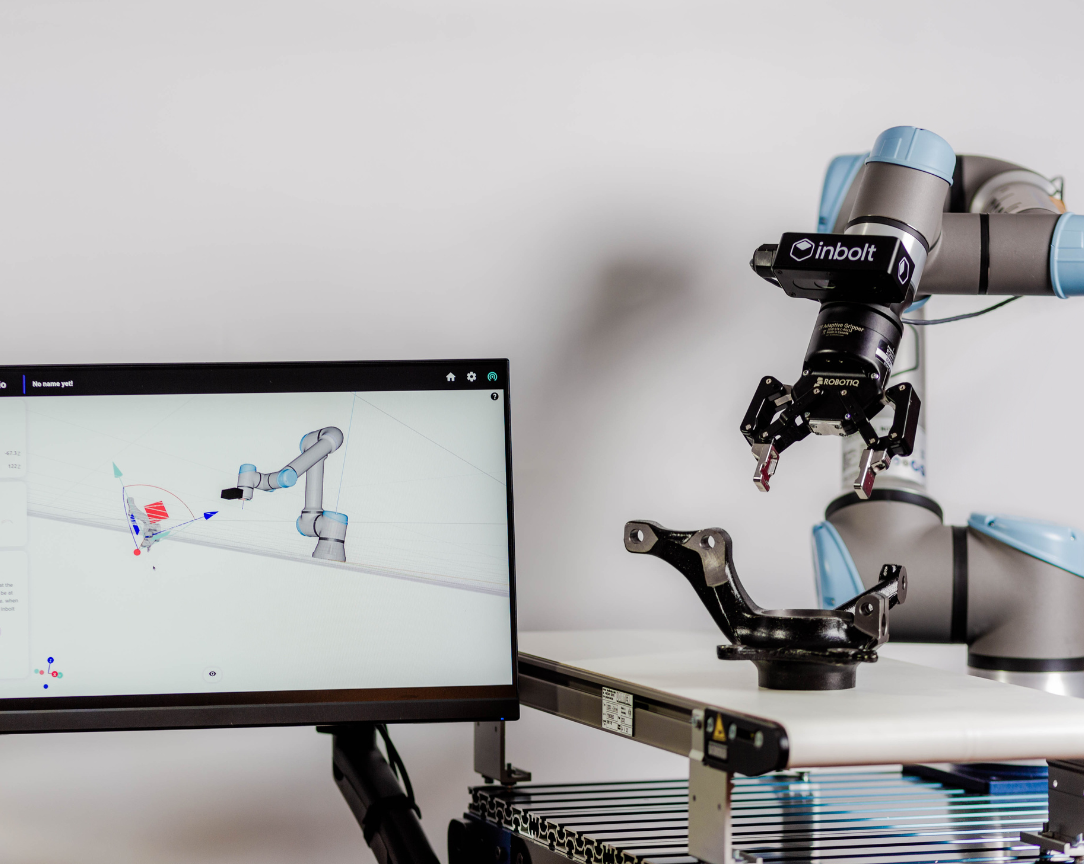
Articles
Sim2Real Gap: Why Machine Learning Hasn’t Solved Robotics Yet
The most successful areas of application for deep learning so far have been Computer Vision (CV), where it all started, and more recently, Natural Language Processing (NLP). While research in Robotics is more active than ever, the translation from research to real-world applications is still a promise, not a reality. But why?