A Beginner's Guide to Assembly Line Automation
Assembly line automation's goal is to boost all aspects of the line to produce goods in a more productive manner. How has it evolved? Let's take a walk.
Before assembly lines, production was done by skilled manual labor and small-scale workshops. Assembly lines marked a significant shift to mass production and standardization, revolutionizing the production process by adding parts to a product in a sequential manner, with each workstation performing a specific task.
The concept of the assembly line was transformed again by Henry Ford in the early 20th century. His introduction of the moving assembly line drastically cut the time needed to assemble a Model T, reducing it from over 12 hours to just about 90 minutes. This innovation not only made cars more affordable but also set a new standard for mass production across various industries.
Assembly line automation has evolved since Ford's time, ranging from simple, repetitive tasks to complex, multi-step processes, transforming manually operated tasks into sophisticated automated operations.
Let’s take a walk.
What’s “Assembly Line Automation”?
Assembly line automation involves using technology and machines to perform tasks that were traditionally done by humans. The goal is to boost all aspects of the line to produce goods faster, more accurately and at a lower cost, while maintaining high standards.
The Basic Components of an Assembly Line
- Conveyor belts are the highways, responsible for moving parts and products from one workstation to another. Modern conveyors can usually adjust speed, detect issues, and make sure everything gets where it needs to go on time.
- Workstations are the workshops within the assembly line. Each one is set up to handle a specific task (putting together parts, checking quality, etc).
- Robots are the pillars, taking over the repetitive and precise tasks like picking and placing parts, welding, painting, etc.
- Control systems are the brains behind the operation, coordinating everything—conveyor belts, workstations, robots—to make sure everything runs smoothly. These systems monitor the entire process while collecting data that can help improve production strategies.
- Quality Control mechanisms are there to make sure products meet high standards, using automated inspection systems with cameras and sensors (or, in certain cases, humans) to spot defects and ensure everything meets the mark.
But even with all this automation, human-machine collaboration is about combining the strengths of both to boost productivity and keep the production process flexible and innovative.
The Types of Automation Systems
Automation in manufacturing comes in various flavors, each suited to different needs and production styles. Let's take a look:
- Robotic Automation: Robotic automation is exactly what it sounds like—using robots to handle tasks that are often repetitive and require precision. Think about robots welding car frames, painting vehicles, or moving materials around a factory.
- Fixed Automation: Fixed automation, also known as hard automation, is great for the high-volume production of a single product. It involves using specialized equipment to perform specific tasks. While it's cost-effective and efficient for producing large quantities, it lacks flexibility. Once it's set up for a particular product, it’s not easy to change. This makes it ideal for industries like automotive manufacturing, where the same item is produced over and over.
- Programmable Automation: Programmable automation is perfect for batch production, where you can reprogram and reconfigure equipment to handle different tasks and products. It's more flexible than fixed automation but still needs some setup time between different batches, making it suitable for industries where production needs to switch between different products, like electronics manufacturing.
- Flexible Automation: Flexible automation, or soft automation, is incredibly adaptable, allowing for quick changes and easy adaptation to different tasks and products. It’s ideal for environments where product designs change frequently, or custom products are made. Flexible automation systems can switch from one task to another with minimal downtime, making them perfect for industries that need to be agile and responsive to market demands.
The Integration of Advanced Technologies
Advanced technologies have become game-changers in recent years, with four notable integrations:
- Vision Systems
Vision systems use cameras and image processing algorithms to perform tasks like quality inspection and object recognition such as robot guidance, helping them to accurately pick and place components, and to ensure that everything is correctly aligned.
- Artificial Intelligence (AI) and Machine Learning
AI and machine learning can analyze vast amounts of data to predict when equipment will need maintenance, ensuring that machines are serviced before they break down. They can enhance quality control and, in some cases, help in process optimization by making real-time decisions.
inbolt’s 3D vision and AI-powered solution makes industrial robots smarter, making it possible for robots to quickly understand and react to their surroundings, facilitating automation on moving assembly lines.
- Internet of Things (IoT)
IoT devices enable machines to communicate with each other, sharing data and coordinating actions. For instance, if a machine detects an issue, it can alert other machines and the central control system to adjust operations; it can monitor and manage inventory, and so on.
Siemens’ Amberg Electronics Plant uses IoT sensors throughout its production line to create a fully digitalized factory, enhancing productivity and flexibility.
- Collaborative Robots (Cobots)
Unlike traditional industrial robots that operate in isolation, cobots work alongside human workers. These robots can take over repetitive and strenuous tasks, and are equipped with advanced sensors and safety features to ensure they can interact with humans safely. Here, both robots and humans contribute to the production process.
- Augmented Reality (AR)
AR technology overlays digital information onto the physical environment, providing real-time assistance to workers. In manufacturing, AR can be used for training new employees, guiding them through assembly tasks, and troubleshooting issues (like using AR glasses to see step-by-step instructions or visualize the internal components of a machine they are working on).
Boeing tried to use AR glasses for wiring and maintenance tasks, allowing workers to see real-time instructions and diagnostics overlaid on their field of view.
Future Prospects of Assembly Line Automation
The evolution of technology will continue to redefine assembly line automation. The convergence of all these new technologies and advancements are bound to create smarter, more efficient and adaptable manufacturing processes over time, allowing industries to remain competitive in a dynamic market.
Last news & events about inbolt
.png)
Articles
Inbolt and FANUC Pioneer Robots that Think and Act on the Fly at Moving Assembly Line Speeds
Inbolt and FANUC are launching a manufacturing breakthrough enabling FANUC robots to tackle one of the most complex automation challenges: performing production tasks on continuously moving parts at line speeds. With Inbolt’s AI-powered 3D vision, manufacturers can now automate screw insertion, bolt rundown, glue application and other high-precision tasks on parts moving down the line without costly infrastructure investments or cycle time compromises.
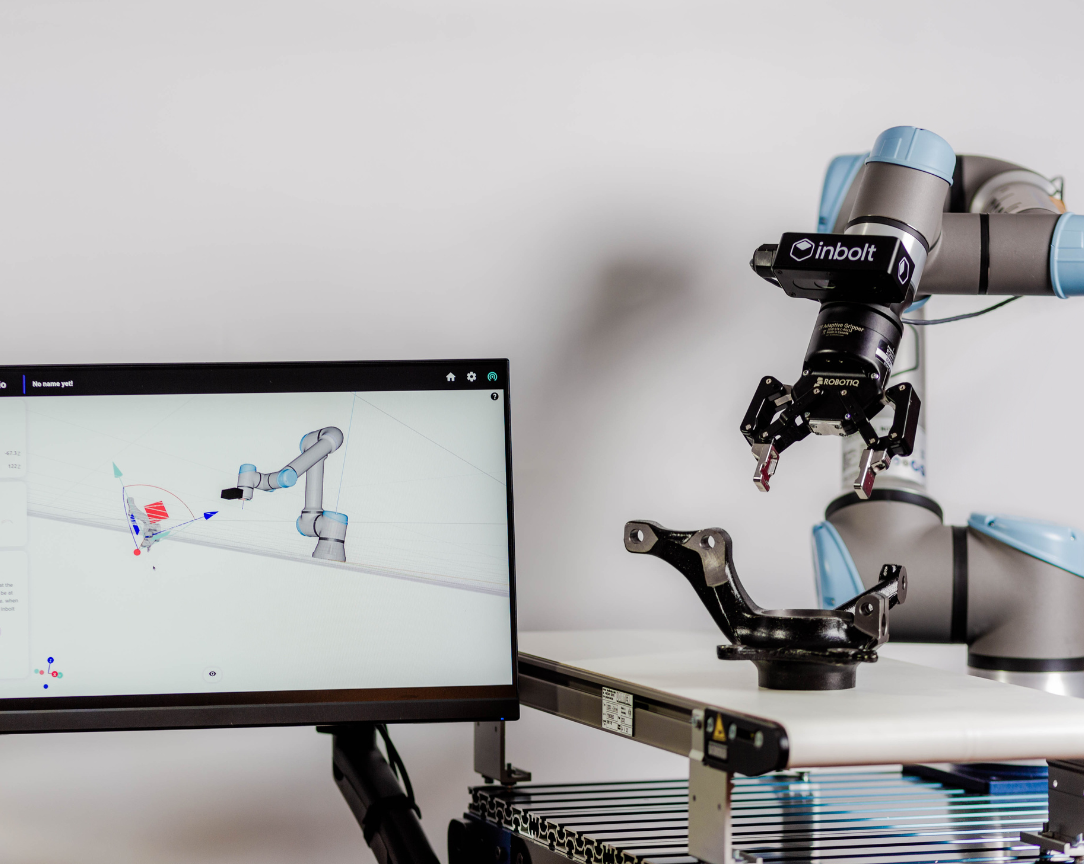
Articles
Sim2Real Gap: Why Machine Learning Hasn’t Solved Robotics Yet
The most successful areas of application for deep learning so far have been Computer Vision (CV), where it all started, and more recently, Natural Language Processing (NLP). While research in Robotics is more active than ever, the translation from research to real-world applications is still a promise, not a reality. But why?