Motion-Based vs. Mission-Based Industrial Robotics: The Emergence of a New Era?
In the world of industrial robotics, two distinct approaches to robot trajectory planning and control have emerged: motion-based and mission-based. Understanding the key differences between these approaches is essential in determining their respective applications and potential for growth.
In the realm of robotics, motion-based systems have long been the standard.
These systems rely on planned, precise and repetitive movements or trajectories to achieve a specific outcome. The environment in which these robots operate must be carefully controlled, with no room for error or unexpected changes.
However, the emergence of mission-based robots is revolutionizing the field, offering a more adaptive and flexible approach to robotics.
This article was inspired by our vision at Inbolt and put into words in a very instructive video from Nick Solar at Drive Capital.
In the world of industrial robotics, two distinct approaches to robot trajectory planning and control have emerged: motion-based and mission-based. Understanding the key differences between these approaches is essential in determining their respective applications and potential for growth.
Motion-Based vs. Mission-Based Industrial Robotics
Motion-based
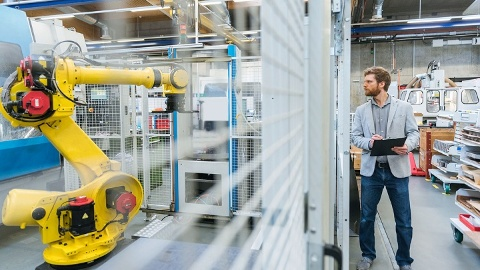
Traditional motion-based robotics demands exacting standards, both in terms of the robot's movements and the environment it operates in. It assumes that the robot's surroundings, as well as the objects it interacts with, are static and predictable. As a result, a predetermined path can be established for the robot to follow, optimizing its movements for efficiency and precision. Such trajectory is usually programmed by controlling in speed and position the robot trajectory in the cartesian space or joint space.
To avoid errors, many measures are put in place to ensure that the movement can be repeated and perfect every time, as a single error can quickly cost several thousands of dollars, or more. In the production environment this usually translates into fixed robot bases, very precise conveyors and fixtures for the parts.
However, this need for perfection which directly translates in quality comes with high initial costs (CAPEX), often requiring the production of vast quantities of identical items to recoup the initial investment. Having so much equipment to handle usually drastically reduces the flexibility of the production line and this is why High-Mix-Lox-Volume SMBs have long remained at the margin of automation.
In the end it is the production environment that adapts to the robot and not the contrary. This is complex and constraining, but now there is a wave of mission-based robots that changes everything.
Mission-based
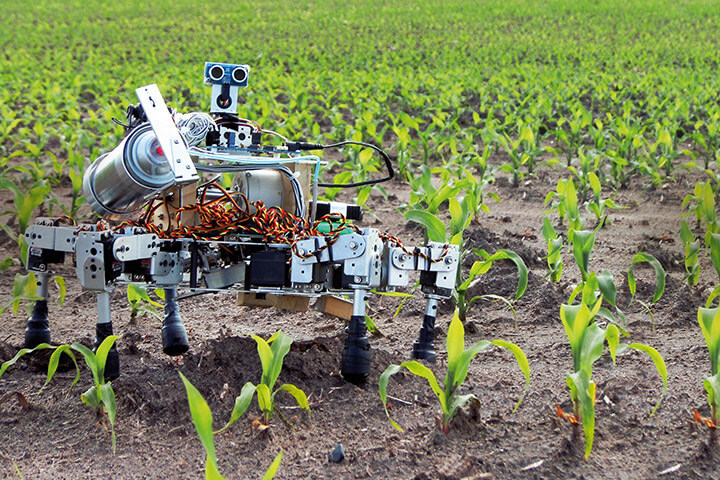
While traditional robotics focuses on planning the robot's trajectory, mission-based robotics focuses on planning the objective and giving the robot the tools to achieve said mission despite the potential roadblocks.
While the general concept is now referred to as Mission-based, the first mention was called Behavior-Based Robotics, or BBR, and has been a hot topic for years, specifically linked to space missions. This is due to the uncertainty and unpredictability of the space environment, which precludes the possibility of creating an optimal path beforehand. Instead, mission-based robots rely on real-time decision-making and adaptability to navigate their surroundings and accomplish their tasks.
The key lies in structuring a behavior-based system that can reconfigure itself on the fly, allowing robots to react quickly and adapt to changing circumstances. This means that the robots must be equipped with sophisticated sensors (2D vision, 3D vision, triangulation) for navigation, environment recognition and often powered by artificial intelligence to make decisions and adapt to changing environments.
Read our article about How to Automate Bin-Picking here.
Mission-based robotics represents a significant step forward in the field of robotics, allowing robots to be more adaptable and better able to accomplish complex tasks in challenging environments. One of the biggest challenges is ensuring that the robots operate safely and reliably in unpredictable and dynamic environments.
We’ll remember that motion-based robotics rely on predetermined trajectories in controlled environments, while mission-based robotics focus on achieving objectives in dynamic environments through real-time decision-making and adaptability.
The Emergence of Mission-Based Industrial Robotics
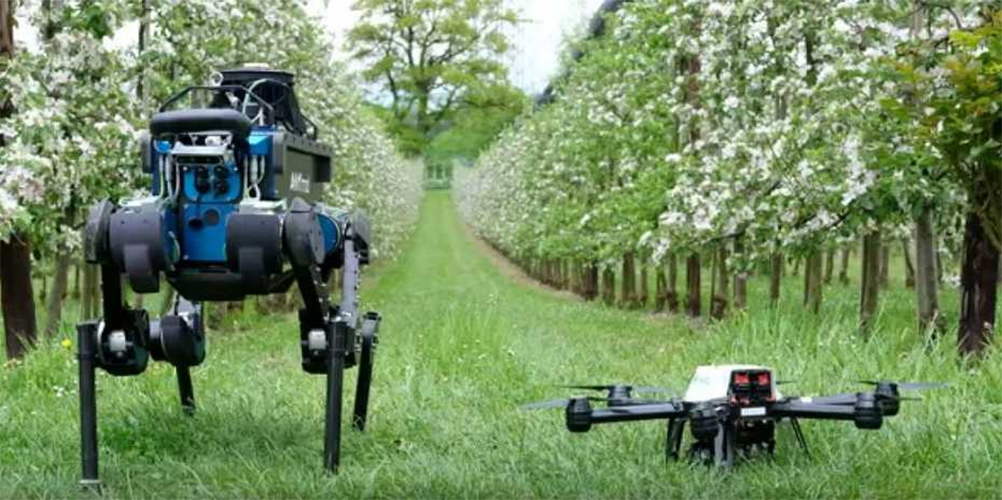
As industries have evolved, so have the demands placed on industrial robots. Complex tasks, dynamic environments, and the need for greater adaptability have given rise to mission-based industrial robotics. Unlike their motion-based counterparts, these robots are designed to make real-time decisions and adapt their movements based on changes in their environment.
Early examples of mission-based robotics in the industry can be traced back to the 1990s with the advent of autonomous mobile robots (AMRs) in warehousing and logistics. These robots were equipped with sensors and algorithms that allowed them to navigate unpredictable environments and make decisions on-the-fly.
More recently, advancements in artificial intelligence, machine learning, and sensor technology such a 3D computer vision have fueled the growth of mission-based robotics in diverse industries.
This trend of mission-based industrial robotics belongs to a future where industrial robotics would be autonomous. Same as for ADAS, where at its highest autonomous level, a car needs to go from location A to location B without human input.
However in the manufacturing industry specifically, autonomous industrial robotics involves a robot performing an industry-specific process without humain input. This is extremely complex, the road is still blurry and the end-goal extremely far (if reachable).
In an ideal world this would entail:
- Identification of parts (very hard for parts, sub-assemblies in discrete manufacturing which by definition have only small datasets)
- Knowing where to apply a predefined process : gluing, picking, etc.
- Choosing the optimal trajectory on the fly : avoiding collision & singularities, minimizing joint impact, optimizing cycle time
- Performing the process and guaranteeing the same quality level as an operator
- Adapting to “unplanned” events and “unstructured” environments
Same as for ADAS, this ideal future has many levels, each of them making automation more flexible and within reach of non-specialists.
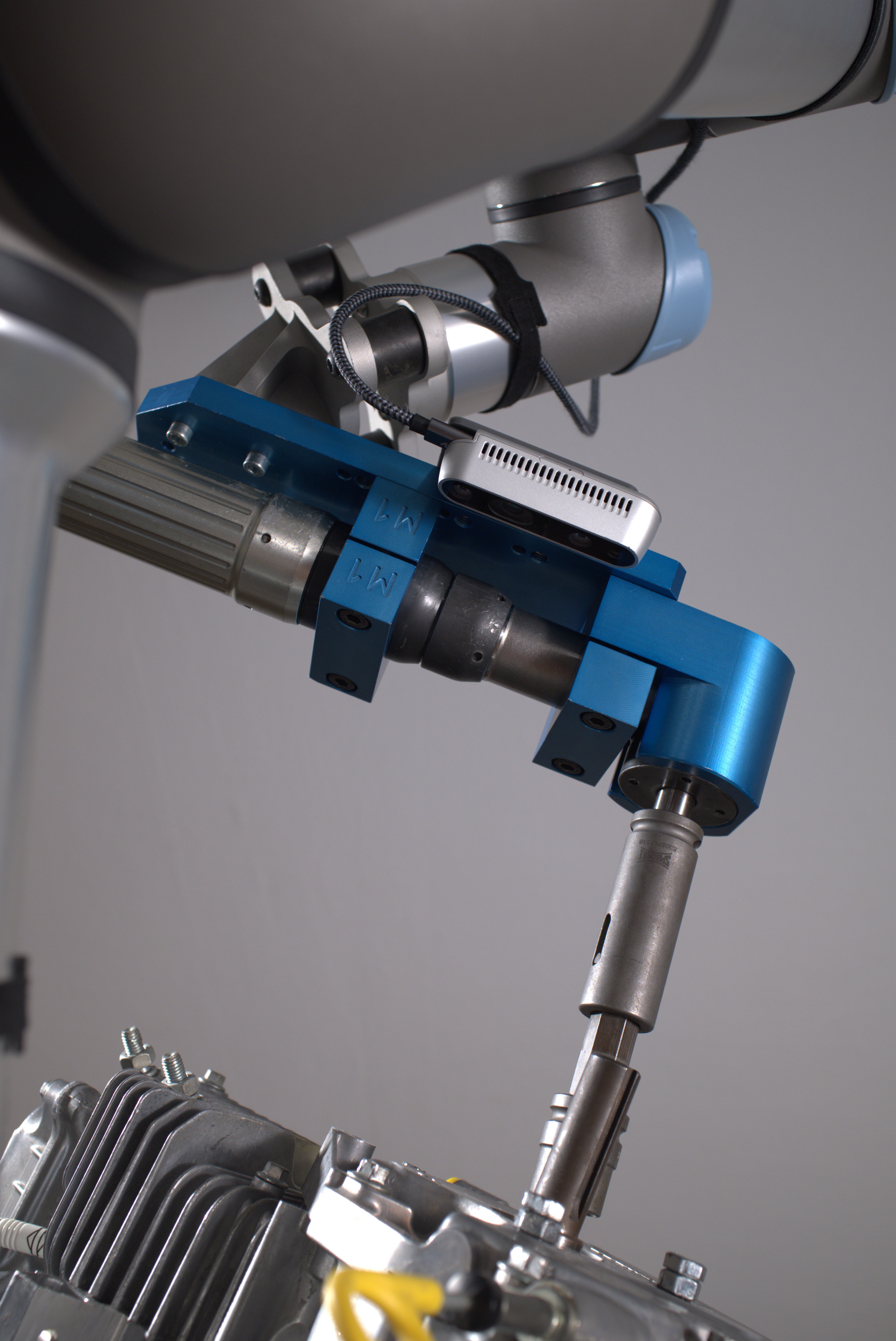
This is the future we are supporting at inbolt with GuideNOW, our real-time robot guidance system based on 3D vision to enable automation in unstructured and unplanned environments.
And we are glad that alongside us are some great companies/startups/scale-ups mapping the way toward autonomous, mission based industrial robotics in the manufacturing industry:
- Path automation
- Vector Robotics
- Moveit
- Nvidia and their new ISAAC simulator
We’ll remember that motion-based industrial robotics have been the standard since the 1960s, but the growing demand for flexibility and adaptability has led to the emergence of mission-based industrial robotics, which have been gaining traction since the 1990s.
Read our article on Automation here.
Will Mission-Based Industrial Robotics Ever Become Ubiquitous?
Despite their potential, mission-based industrial robots have yet to achieve the same level of adoption as their motion-based counterparts.
Motion-based industrial robots are employed in a variety of industries. It is still, by far, the norm within industrial robotics. After all, for any mission requiring low mix, high volume, motion based robotics tends to be perfectly adequate. The cost to implement remains high, but the profit over time does cover the initial investment.
However, the past years have seen a switch from low mix to high mix, and from high volume to low volume, in order to sustain the growing trend of customisation and personalisation.
In order for mission-based robotics to become ubiquitous, several challenges must be overcome:
- Cost: Developing and implementing mission-based robots can be expensive due to the need for advanced sensors, computing power, and sophisticated algorithms. As these technologies become more accessible and affordable, the adoption of mission-based robots is likely to increase.
- Standardisation: The lack of standardised platforms, protocols, and interfaces for mission-based robots can hinder their integration. But as industry-wide standards are slowly starting to be discussed, we should see smoother implementation and wider adoption of these systems throughout the industries.
- Safety and Reliability: Ensuring the safety and reliability of mission-based robots in dynamic environments is a critical concern for potential adopters. Continued improvements in sensor technology, machine learning algorithms, and control systems will be essential for building trust in mission-based robots. Indeed, if some missions require humans to evolve in close proximity to robots, robots need to have a fail-proof system to stop them from accidentally harming the humans they work closely with.
As technology keeps advancing and industries crave more adaptability, industrial robotics is likely to experience a shift towards mission-based systems. This development presents an exciting opportunity to push the boundaries of robotics even further. By striking the right balance between robotic autonomy and human safety, we can usher in a new generation of robots that could tackle the evolving demands of customers that we've witnessed growing over the past few years.
Last news & events about inbolt
.png)
Articles
Inbolt and FANUC Pioneer Robots that Think and Act on the Fly at Moving Assembly Line Speeds
Inbolt and FANUC are launching a manufacturing breakthrough enabling FANUC robots to tackle one of the most complex automation challenges: performing production tasks on continuously moving parts at line speeds. With Inbolt’s AI-powered 3D vision, manufacturers can now automate screw insertion, bolt rundown, glue application and other high-precision tasks on parts moving down the line without costly infrastructure investments or cycle time compromises.
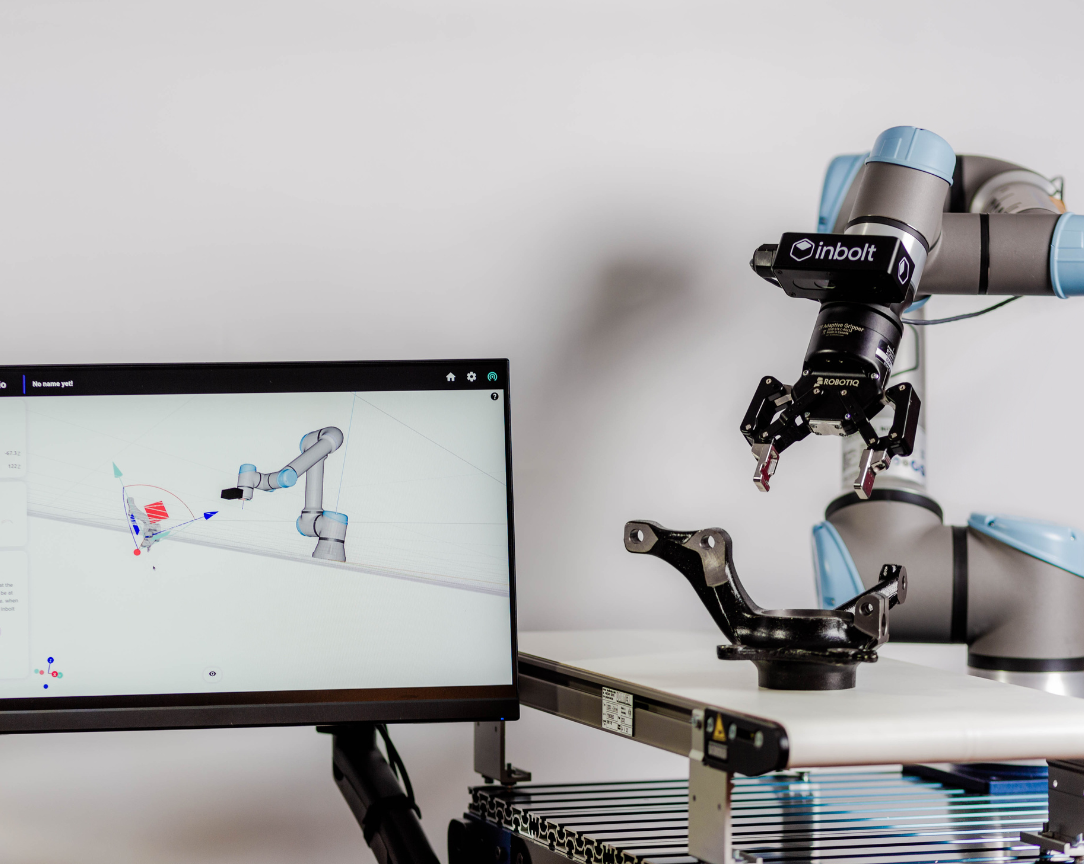
Articles
Sim2Real Gap: Why Machine Learning Hasn’t Solved Robotics Yet
The most successful areas of application for deep learning so far have been Computer Vision (CV), where it all started, and more recently, Natural Language Processing (NLP). While research in Robotics is more active than ever, the translation from research to real-world applications is still a promise, not a reality. But why?