2D Vision vs 3D Vision
The choice between 2D and 3D vision technologies often sparks debate; however, this is not necessarily an "either-or" decision. The debate between 2D and 3D machine vision systems is often a matter of application-specific requirements, as each application offers unique advantages and limitations. Let’s delve into why both 2D and 3D vision systems have distinct roles in manufacturing, and why neither is poised to render the other obsolete.
Should you choose 2D-vision or 3D-vision sensors for your robots?
In the wake of Industry 4.0, manufacturers increasingly rely on advanced vision systems for automation tasks from bin-picking to tightening, from glue application to maching tending.
The choice between 2D and 3D vision technologies often sparks debate; however, this is not necessarily an "either-or" decision. The debate between 2D and 3D machine vision systems is often a matter of application-specific requirements, as each application offers unique advantages and limitations. Let’s delve into why both 2D and 3D vision systems have distinct roles in manufacturing, and why neither is poised to render the other obsolete.
2D Vision: The Dependable Workhorse
2D vision systems capture images in only two dimensions: width and height. They essentially analyze objects as flat, planar entities.
Strengths
- High Contrast Sensitivity: 2D vision excels in high-contrast scenarios or when the inspection of texture or color is paramount.
- Dominant Technology: For many machine vision tasks, 2D remains the dominant technology, as it was the easiest to put in place and has been around since the 1980s.
- Optimal for Static Objects: 2D cameras are suitable for inspecting objects that aren't moving, like in pick-and-place operations or for parts moving on conveyors using [line-scan](https://blog.robotiq.com/1d-2d-3d...-what-kind-of-vision-system-should-i-use-for-my-application) cameras.
- Cost-effective: Typically, 2D vision systems are less expensive than their 3D counterparts, making them an attractive option for many applications.
- Speed: The simplicity of 2D imaging means that these systems can often process items at a faster rate.
2D machine vision systems generally requires a highly-controlled environment with standardized viewpoints and precise lighting (creating high contrast and eliminating shadows). The more structured the environment, the better.
Limitations
- Environment Sensitivity: 2D systems necessitate highly-controlled environments with standardized viewpoints and carefully calibrated lighting that maximizes contrast while minimizing shadows.
- Lack of Depth Information: 2D systems can't evaluate the depth or volume of an object.
- Sensitivity to Lighting: Changes in lighting can significantly affect the system's performance.
There are certain limitations, however, that come with the territory. 2D is prone to limitations, especially when it comes to occlusion, fixed depth of focus, sensitivity to ambient light, and contrast variations.
For which Application?
For applications where an object moves on a dynamic line, technologies like laser scanners or line-scan cameras usually suffice. They will gather "line images" to stitch together into a 2D representation for analysis. When inspecting stationary objects or performing pick-and-place operations, a standard 2D camera generally meets the requirements.
In fields where high contrast or texture and color inspection is critical, 2D vision dominates. That being said, keeping lighting the same at all time remains a particularly challenging variable to control.
Read our article on Computer Vision in Robotics.
3D Vision: The New Kid on the Block
3D vision systems capture images in three dimensions: width, height, and depth. This is particularly useful for applications that involve the manipulation of complex objects or require precise measurements.
Strengths
- Adaptable to Non-rigid Objects: 3D scanners are proficient with non-rigid objects. Indeed, certain challenges can arise when working with specific objects or under certain conditions in 3D vision (reflective or uniform surfaces, for example).
- Robust to Lighting Changes: The performance is less affected by variations in lighting.
- Depth Information: 3D systems can measure the volume, width, and height of objects, providing a more complete picture.
- Complex Object Recognition: 3D vision is better suited for recognizing objects that require a high degree of precision.
- Robotic Guidance: Robot arms that need to pick objects from bins or place them in specific orientations use 3D vision to understand the spatial orientation and depth of the items.
Unlike "blind" robots limited to repetitive tasks, 3D computer vision systems allow for adaptability. The 3D camera can “see” variations in the physical environment, and, sometimes, inform the robot of this variations, thus helping it rearrange its trajectory. This the case, for instance, of inbolt’s technology. Using 3D cameras in these cases results in increased flexibility, utility, and velocity in manufacturing processes.
Reach out to us to learn more about how you can automate your automation process.
Limitations
- Complexity: 3D systems are generally more complex to implement and require more processing power.
- Cost: The hardware and software involved are usually more expensive.
For which Application?
For applications that require the robot to be smart.
Why Both Systems Have a Place in Manufacturing
Versatility vs. Specificity
While 3D systems provide more data and can handle more complex tasks, not all manufacturing needs demand such intricacy. For instance, sorting flat metal sheets by thickness can be efficiently done with 2D vision, while ensuring the correct alignment of a 3D-printed component within an assembly would require 3D vision.
Integration with Existing Systems
Companies that already employ 2D vision systems might find it more cost-effective to continue using them for tasks they are suited for, integrating 3D systems only where depth perception is necessary.
Cost and Maintenance
While 3D systems offer comprehensive insights, they also come with higher initial costs and can be more complex to maintain. On the other hand, 2D systems are often easier to set up, calibrate, and maintain.
While 3D vision technology might seem like the natural successor to 2D systems, it's evident that both have distinct strengths that cater to different needs within the manufacturing industry. Generally speaking, integrators and robot distributors will have an idea, however vague, of the best type of vision for your manufacturing process.
Neither 2D nor 3D vision systems are universally superior; each has its place depending on the application at hand. They are complementary technologies, each solving unique challenges in the modern manufacturing landscape.
Last news & events about inbolt
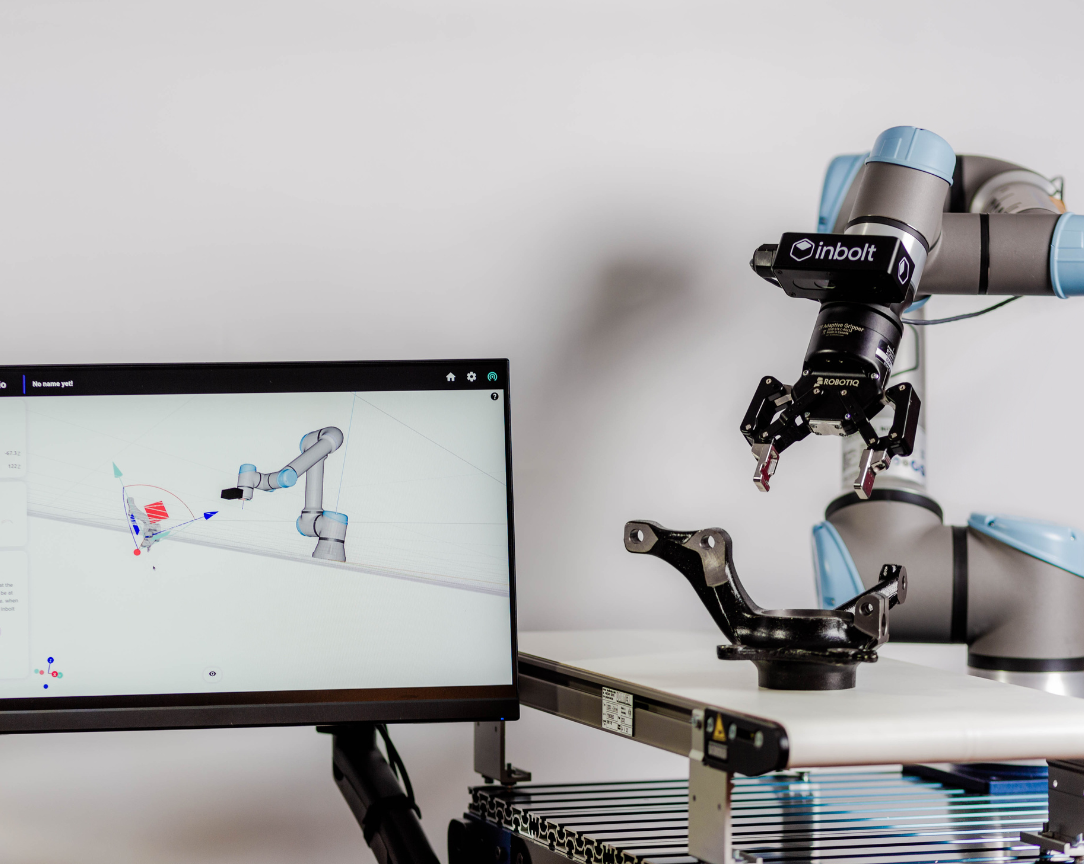
Articles
Sim2Real Gap: Why Machine Learning Hasn’t Solved Robotics Yet
The most successful areas of application for deep learning so far have been Computer Vision (CV), where it all started, and more recently, Natural Language Processing (NLP). While research in Robotics is more active than ever, the translation from research to real-world applications is still a promise, not a reality. But why?
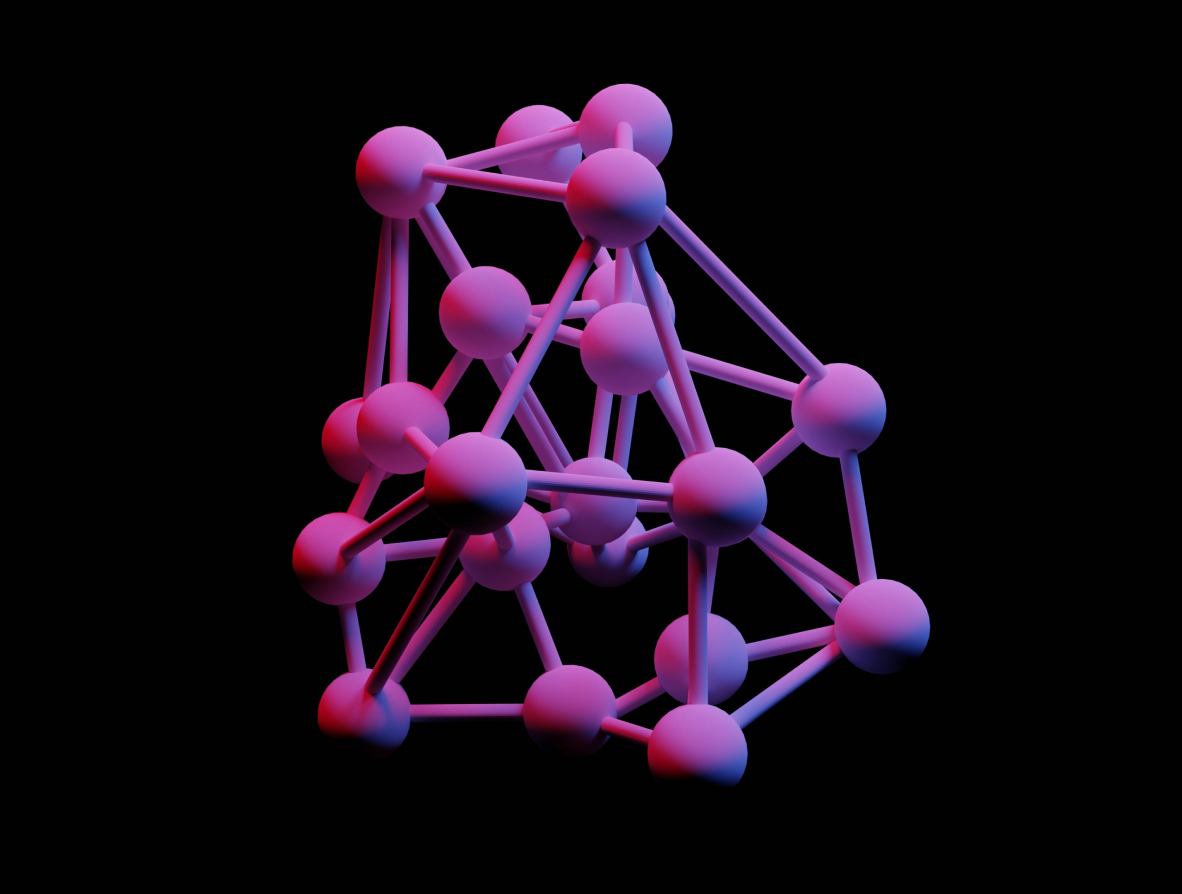
Articles
Exploring the potential of LLMs in robotics: an interview with Louis Dumas
Robotics has always been at the forefront of technological advancement, but translating human ideas into robotic actions remains one of its greatest challenges. In an interview with Louis Dumas, co-founder and CTO of inbolt, he shared his insights into the transformative potential and current limitations of Large Language Models (LLMs) in the robotics field.